Home
Perspectives
The woman who shapes products
The woman who shapes products
Join our UX team!
Are you passionate about human-centered design? Then join our User Experience team in India and design medtech that solves real-life challenges!
The words "Maker Space" are written in large letters on the wall of the workshop where our product designers make their initial simple prototypes – often from foamcore board and glue. And, for this job, you really do have to be a "maker":
"Product designers should be born with a measure of artisanal talent," says Stefanie Gügel-Wild, laughing. But creating a product design takes far more than just that, particularly when it comes to complex medical devices.
Stefanie's first medical technology project close to her heart was to design an incubator for preterm infants. She developed the design as part of her thesis while she was at the Schwäbisch Gmünd University of Applied Design, studying industrial and product design : "At university you learn the basic design principles and processes. And this should put you in a position to design any product," explains the designer.
Stefanie's first jobs involved an appropriately diverse range of work: She designed children's furniture, toys, and accessories for a manufacturer of children's products. Then for a number of years it was electronic devices such as televisions, radios, and speakers as well as kitchen appliances for a major consumer electronics producer. Yet, the complexity of medical devices never ceased to fascinate her, leading her to join Siemens Healthineers in 2019, where she works today on the Design Team as Lead Industrial Designer.
Industrial and product design
Why I wanted to work as a product designer in the medical technology field? Because I want to design products that have real importance for people.
Stefanie Gügel-Wild
Lead Industrial Designer, Siemens Healthineers
How are new products created at Siemens Healthineers? As Stefanie explains in her #Futureshaper interview, technical developers from the various business segments usually approach the Design Team once planning for a new product is underway. "It's important first of all to understand what precisely the problem is that we're trying to solve with this product?"
#Futureshaper
Watch now: #Futureshaper video portrait of Stefanie
The design of a product never just serves some "decorative" end in itself: Its form follows the function that the product has for users and patients. All design considerations focus on serving people. "User experience" is the keyword here: The product should be intuitive to operate, and offer its users real added value. This is why every project begins with a detailed user survey, for example in hospitals or among physicians. What specific requirements do users have?
Product design starts with research
Besides the information they glean from user surveys, product designers need wide-ranging background knowledge and further research. Working in collaboration with the technical developers and colleagues from the User Experience Team, they clarify questions like: What installation space do the technical components require inside the product? What operating elements are needed? What processes will later be used to manufacture the product and its individual components? What requirements arise from hygiene regulations? And, how much can the final product cost?
User Experience Team
Our UX Team is looking for support! Curious to learn more? View the current recruitment postings here:
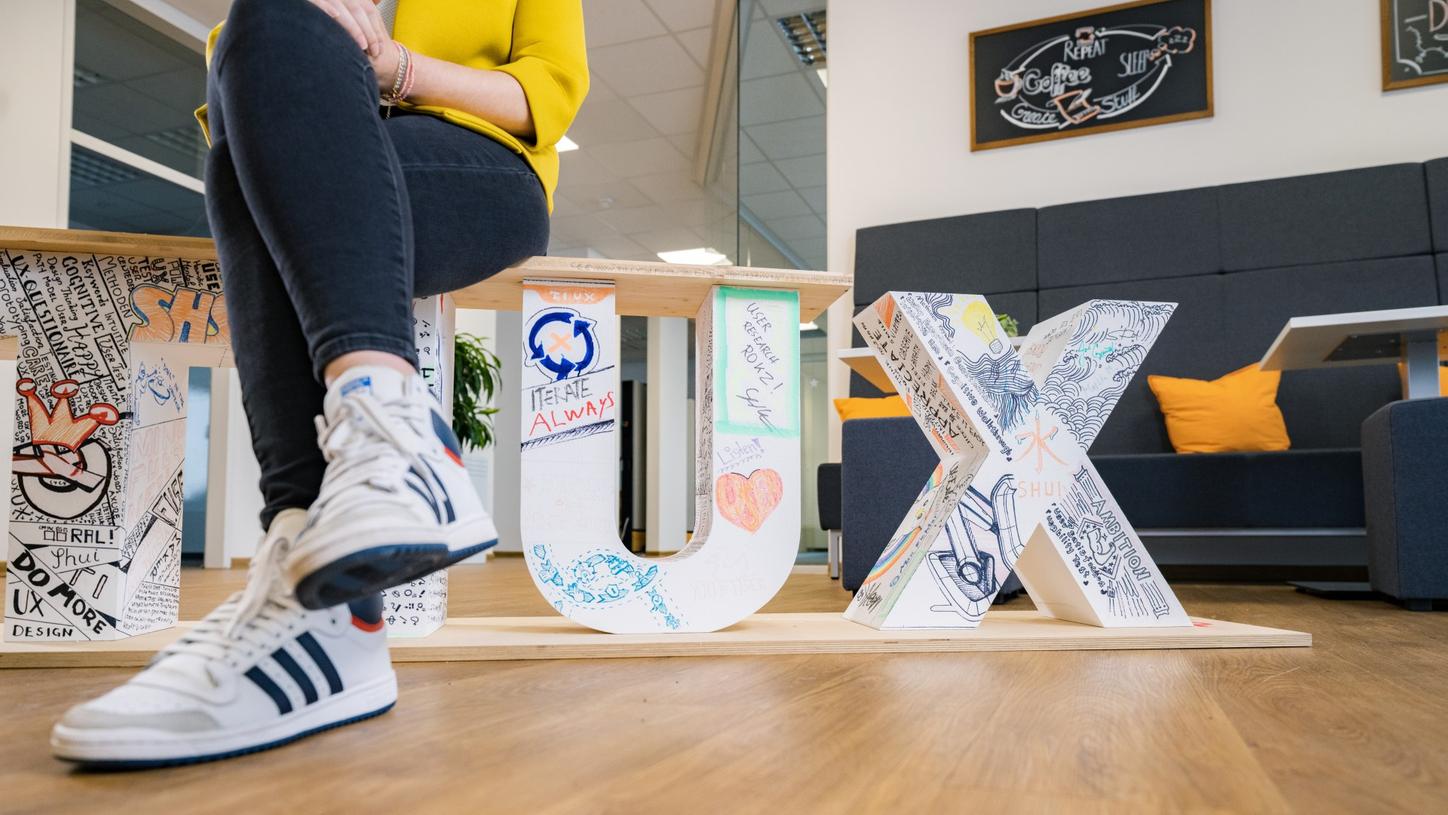
It´s all about UX
All product design considerations focus on user experience (UX).
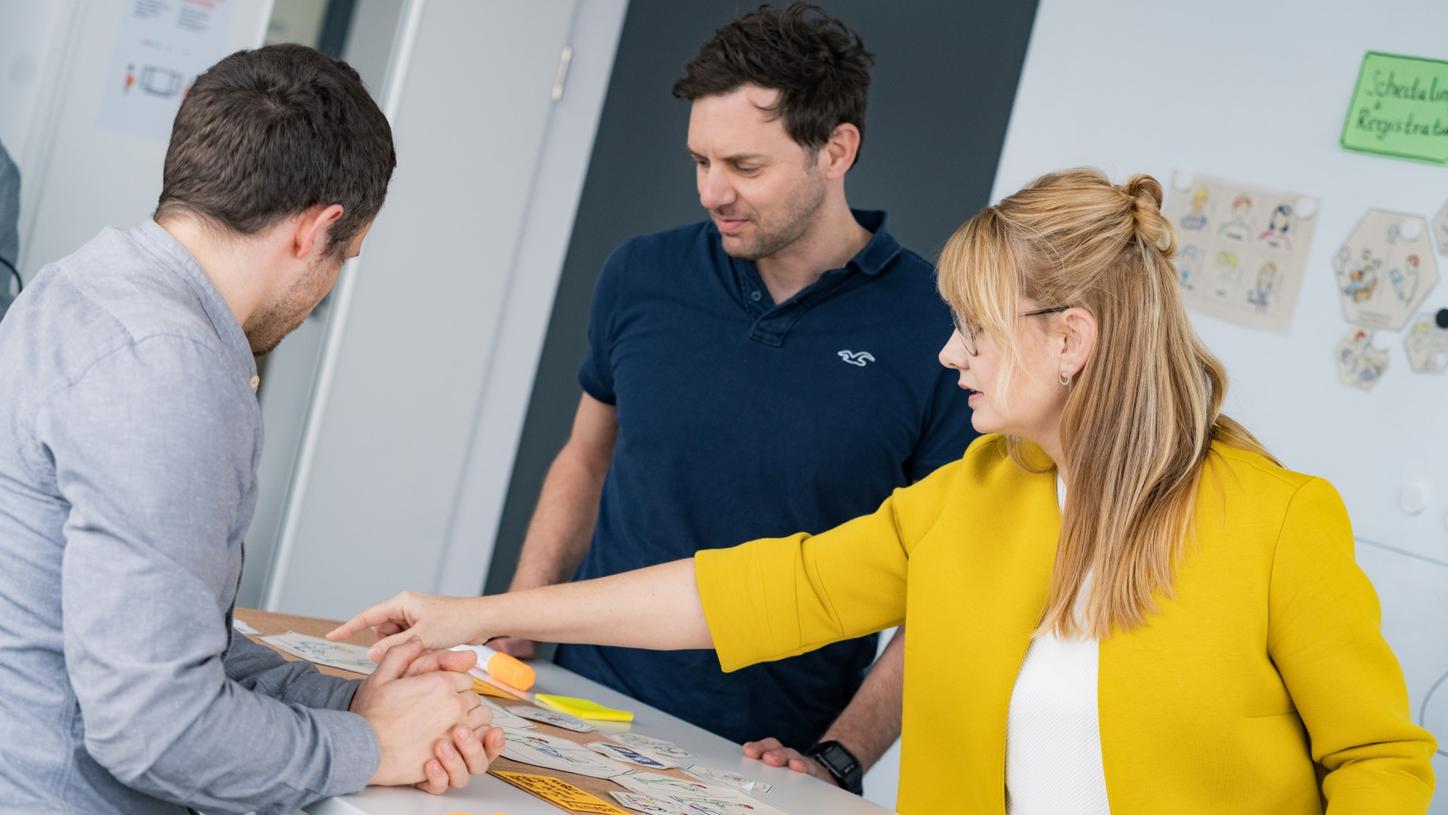
Stefanie together with Timo Freitag from the UX Operations Team and Industrial Designer Sebastian Dennert. Every product design is created by a team of experts.

It starts with a sketch
The initial product visualization is often a simple hand-drawn sketch. But, as Stefanie explains, the basic design concept must be clearly recognizable.
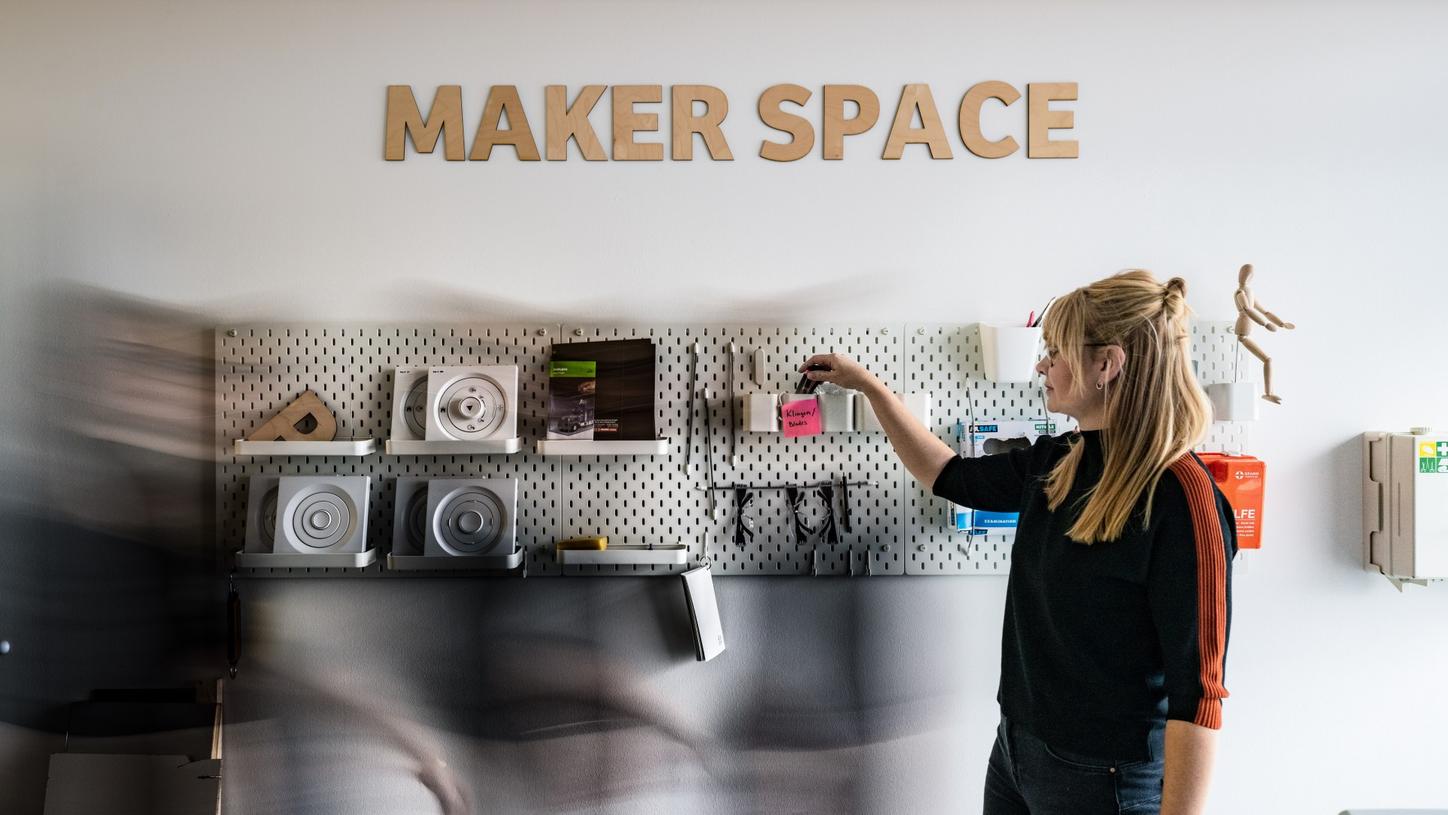
The home base of "makers"
"Maker Space" is the name of the industrial designers' in-house workshop. Here's where the team builds the first product prototypes.
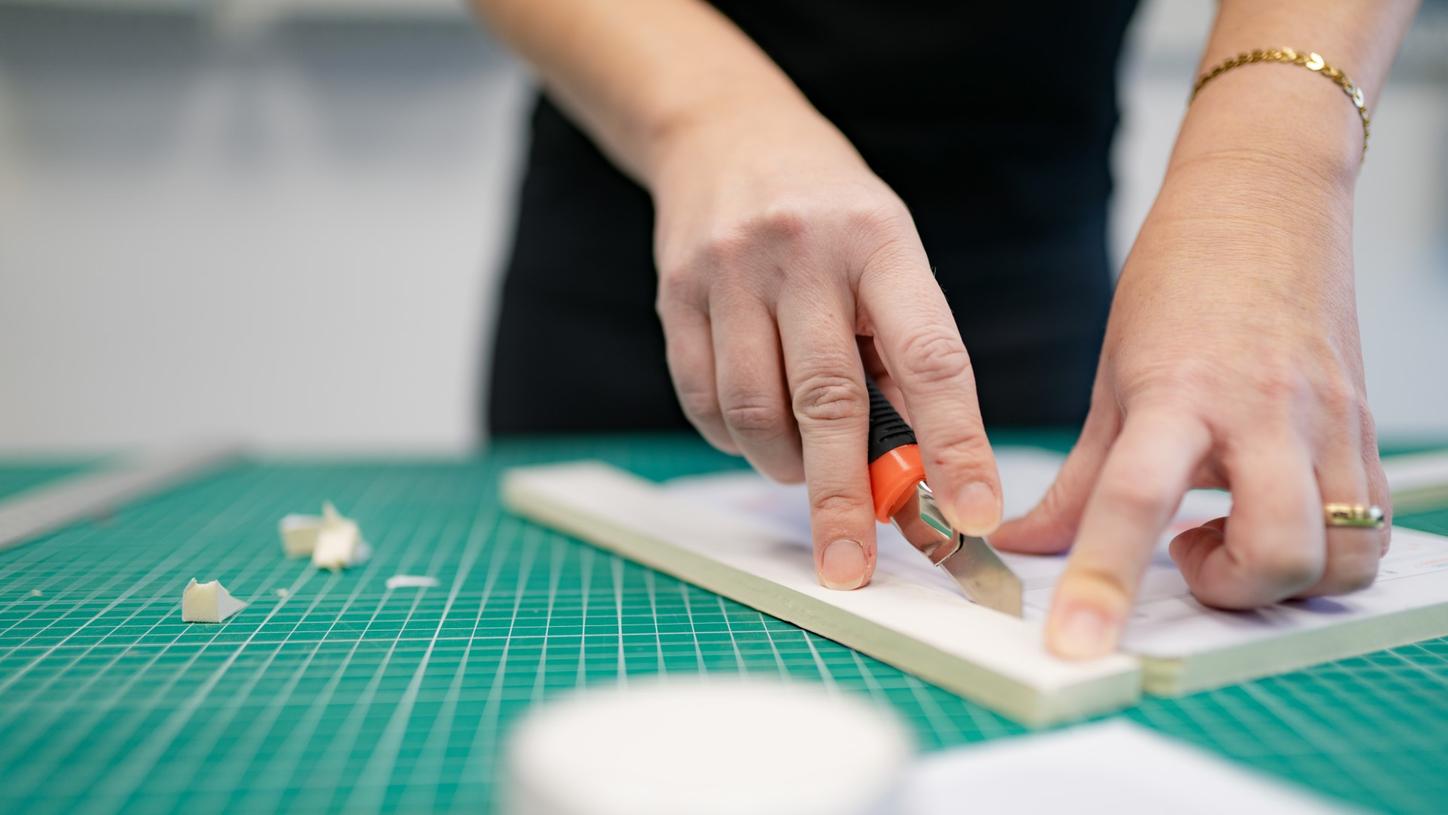
Genuinely hand-made
The designers often construct the first sub-component prototypes of the planned product from foamcore board.
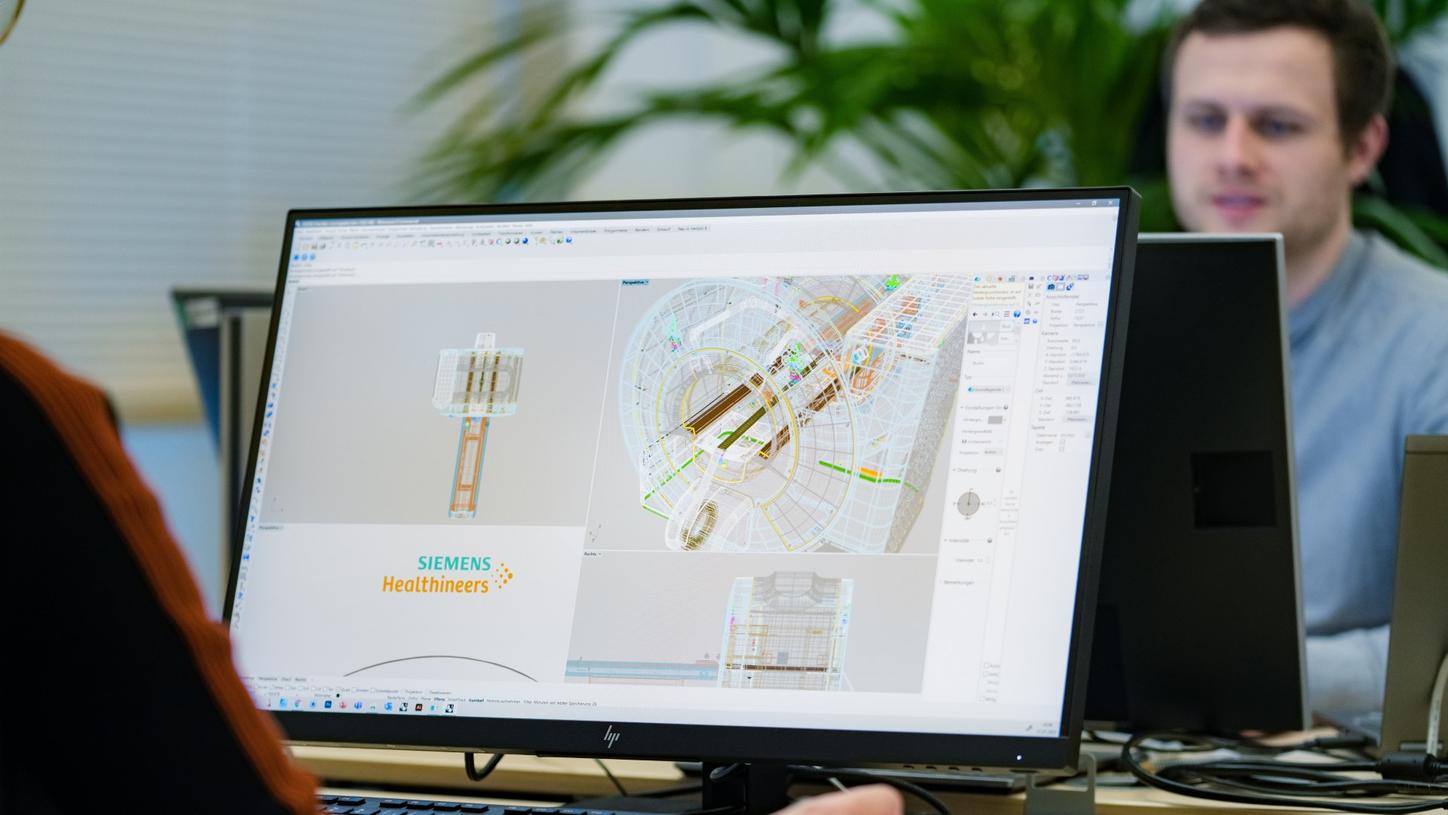
Digital 3D models
They generate digital product models using computer-aided 3D modeling software.
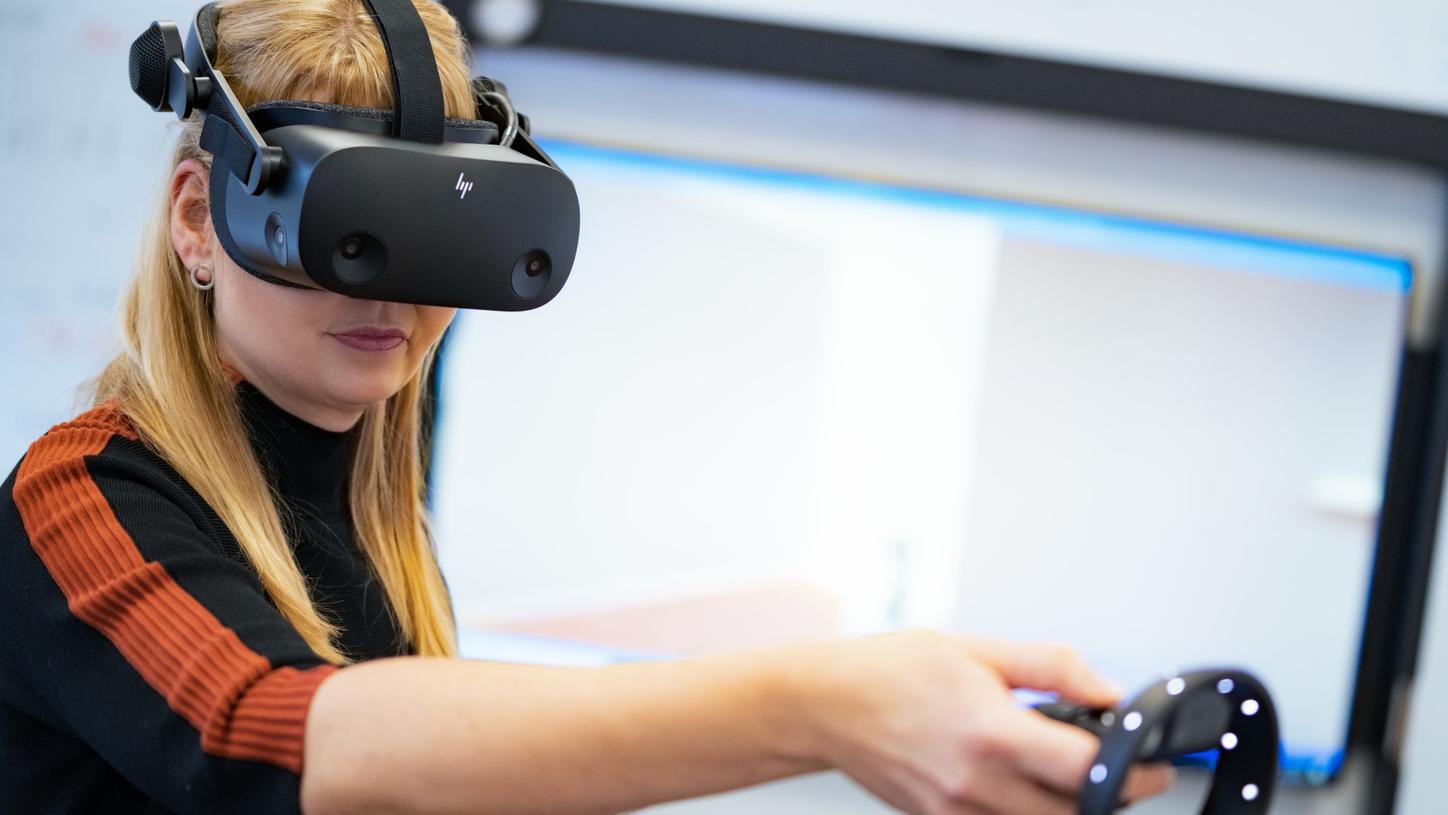
Diving into virtual reality
The team uses virtual reality (VR) to create a very realistic impression of the future full-size product.
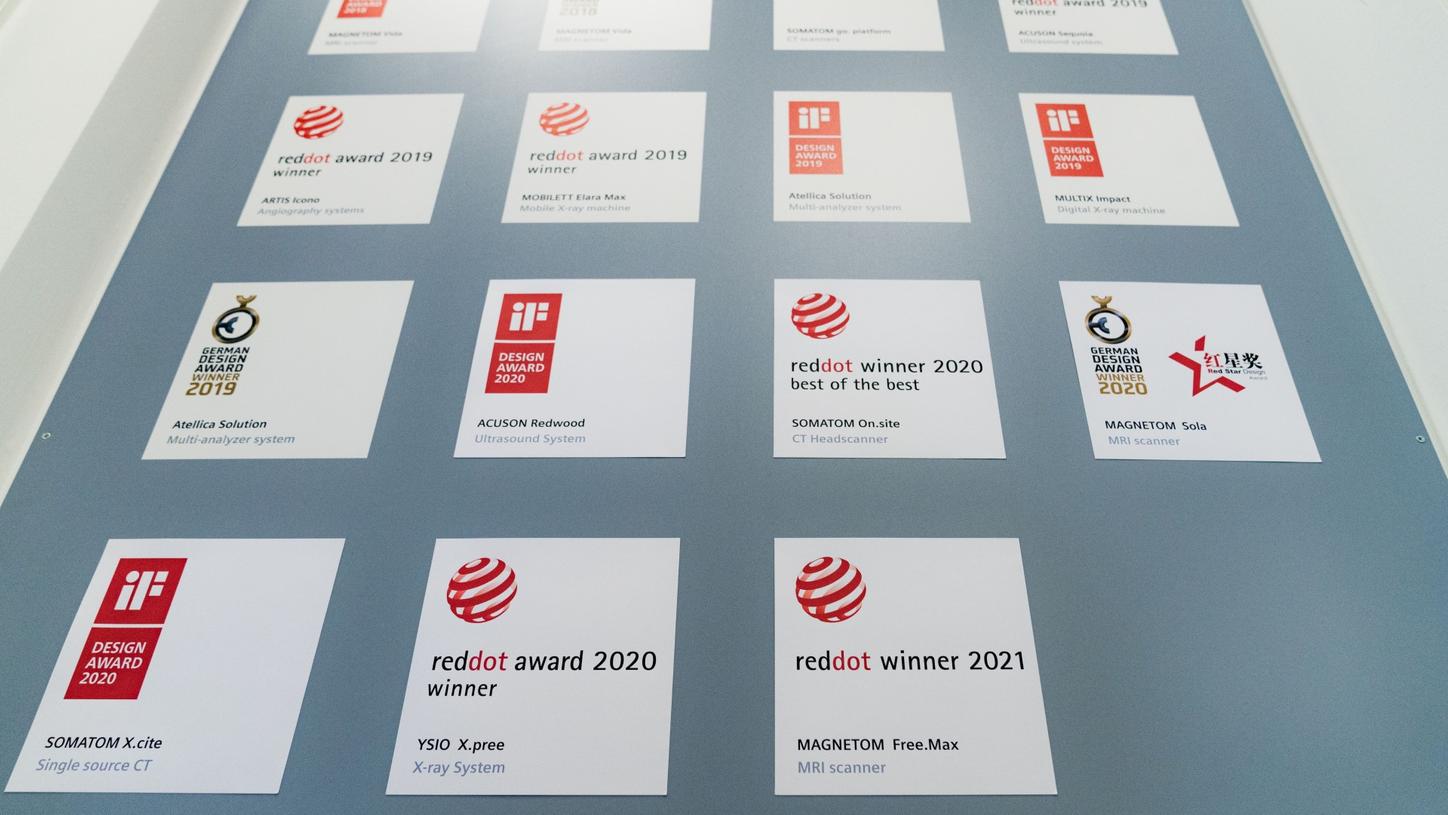
Wall of fame
Awards won by the Industrial Design Team hang on the Award Wall. The Red Dot Design Award won for the MAGNETOM Free.Max was added in 2021.
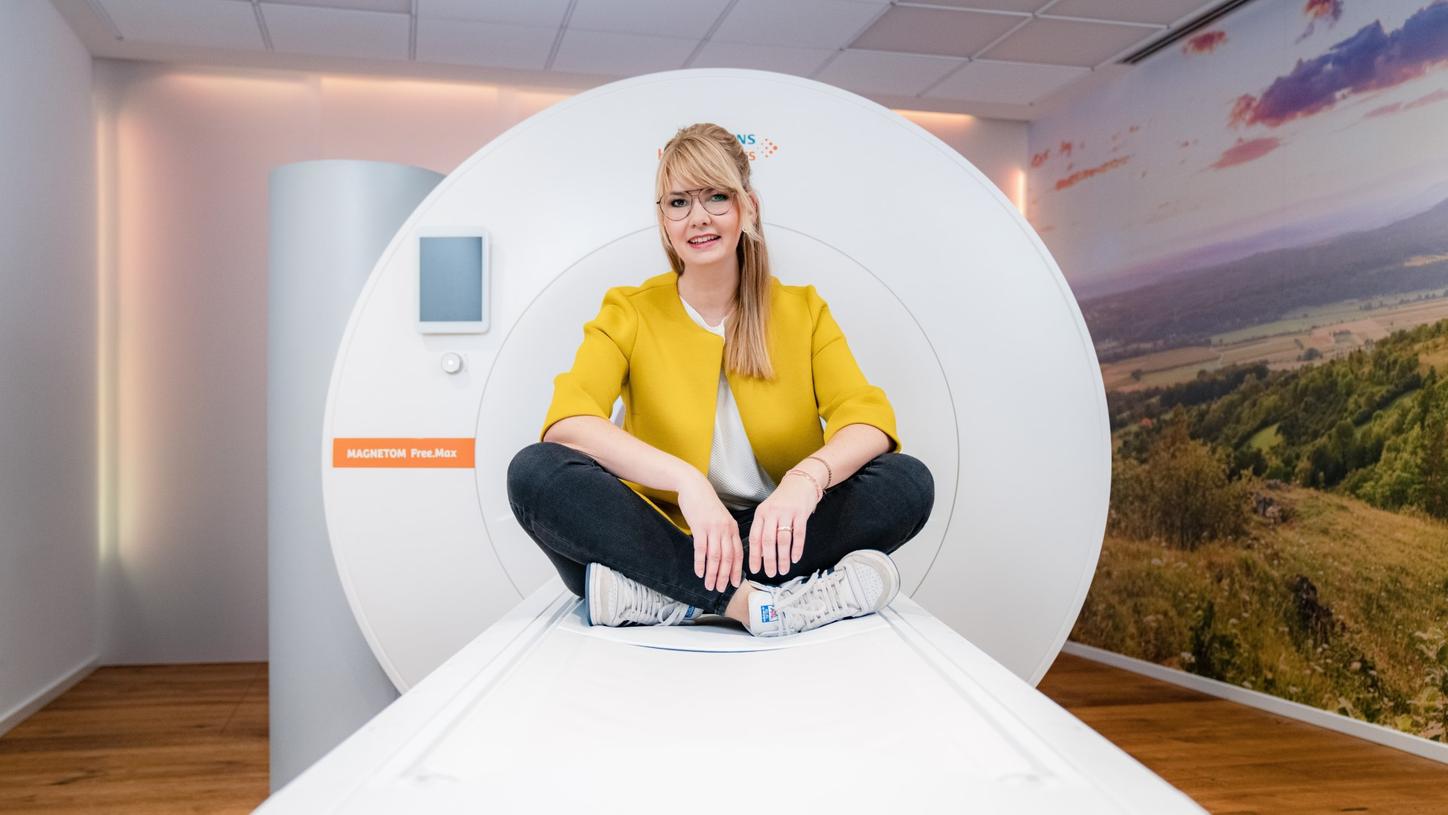
Outstanding design
Stefanie was the design lead responsible for designing the award-winning MRI scanner.
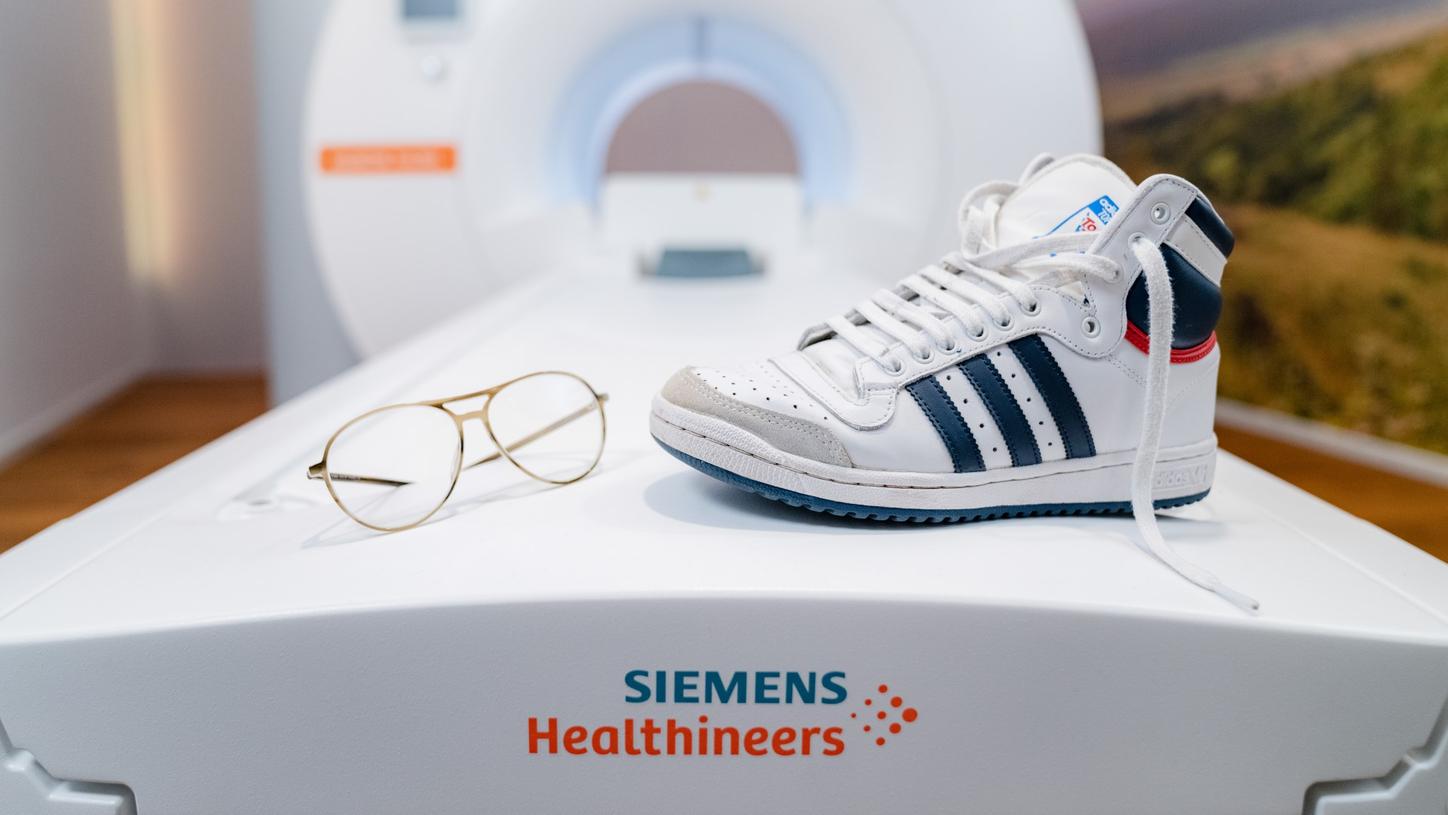
"Designer" outfit
Still life with style: A pair of statement glasses and sneakers are part of Stefanie's standard "work attire".
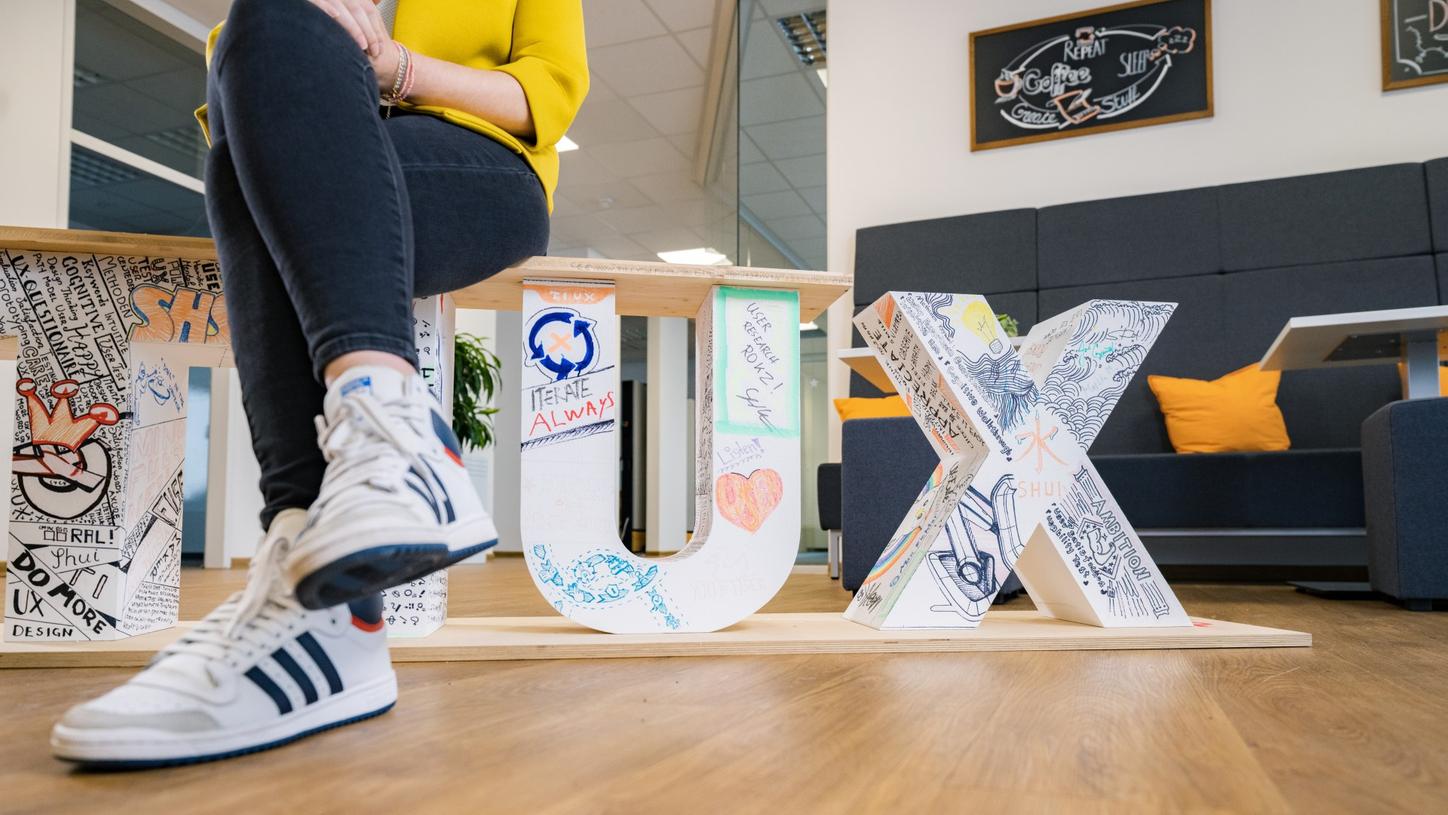
It´s all about UX
All product design considerations focus on user experience (UX).
This is where Stefanie's work really kicks into high gear. And it takes endurance: "From the first draft to market launch, the process of developing a medical technology product takes two to three years on average," explains the 42-year-old.
During this time frame, the product designers build any number of various models, called mockups. This process involves not only cutting, gluing, and screwing, but also simulating and testing in digital 3D spaces using software for computer-aided 3D modeling, or even virtual reality headsets.
The team pursues its development of new product designs by applying a specially defined system based on the "design thinking" method :
Design thinking
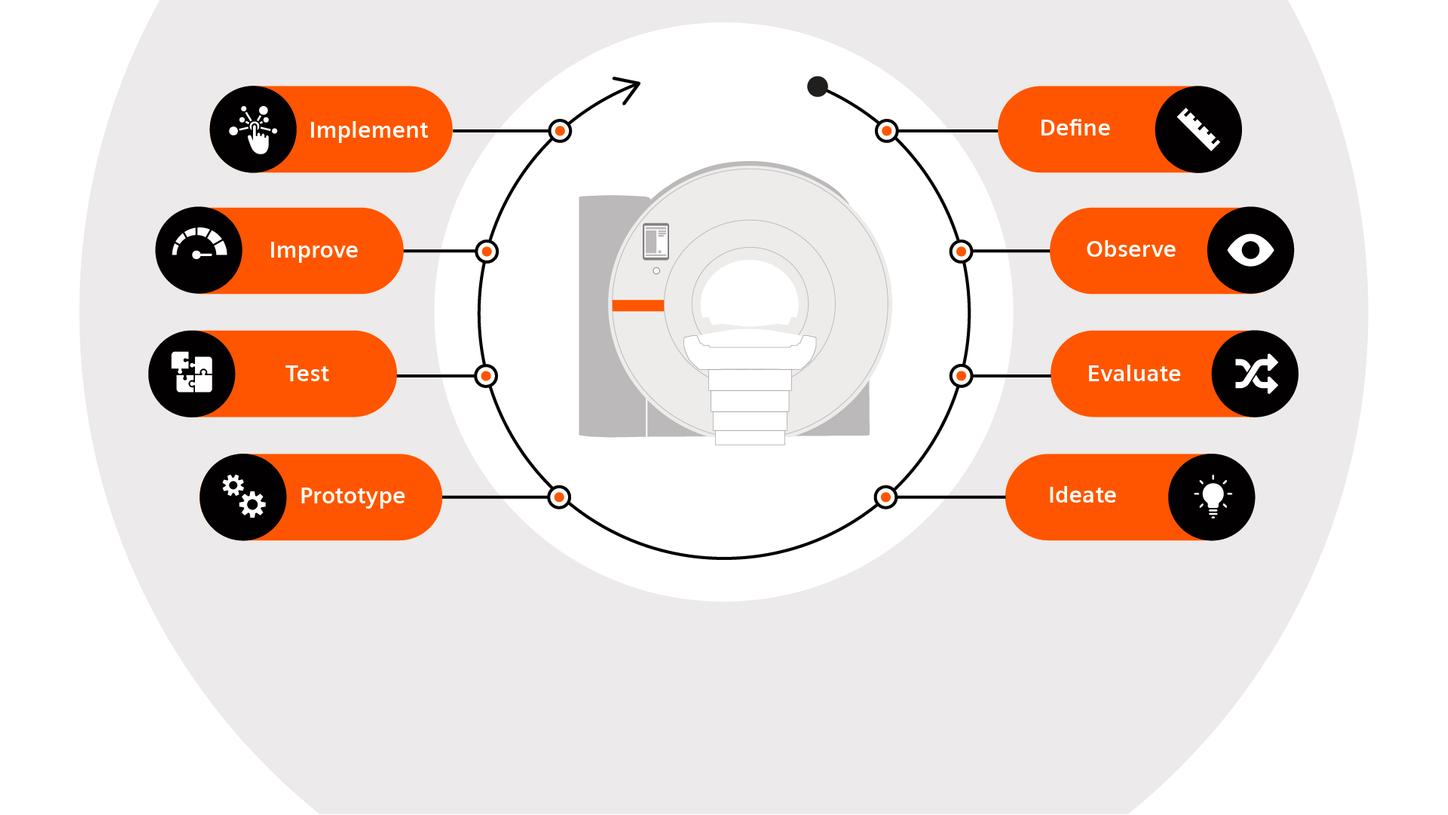
Extensive preliminary considerations, modeling, and testing are needed before products take on their final appearance. Everything is based on the "design thinking" approach.
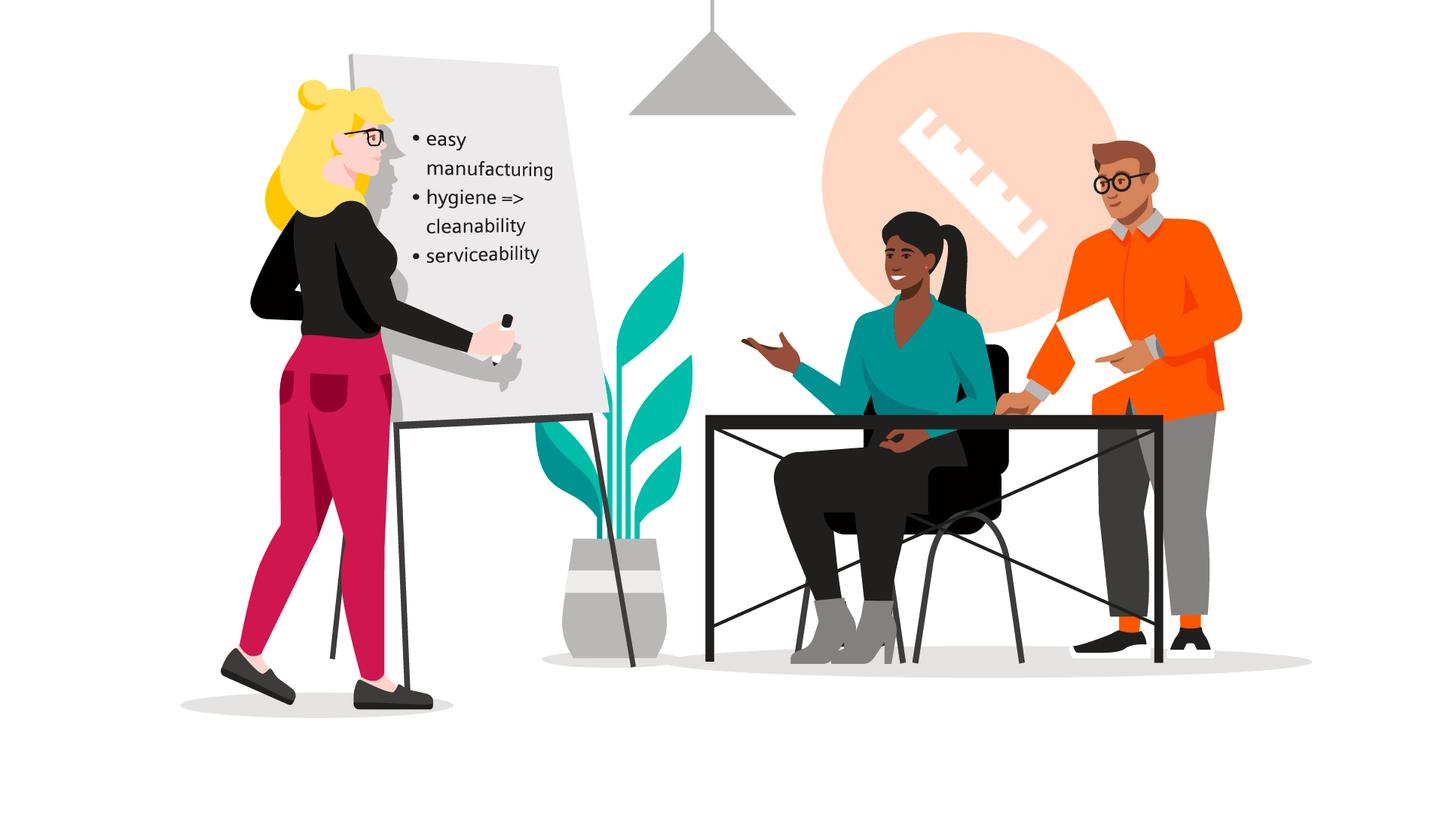
First, the team defines the basic prerequisites and strategy. What problem will the product solve? What parameters must the product fulfill?
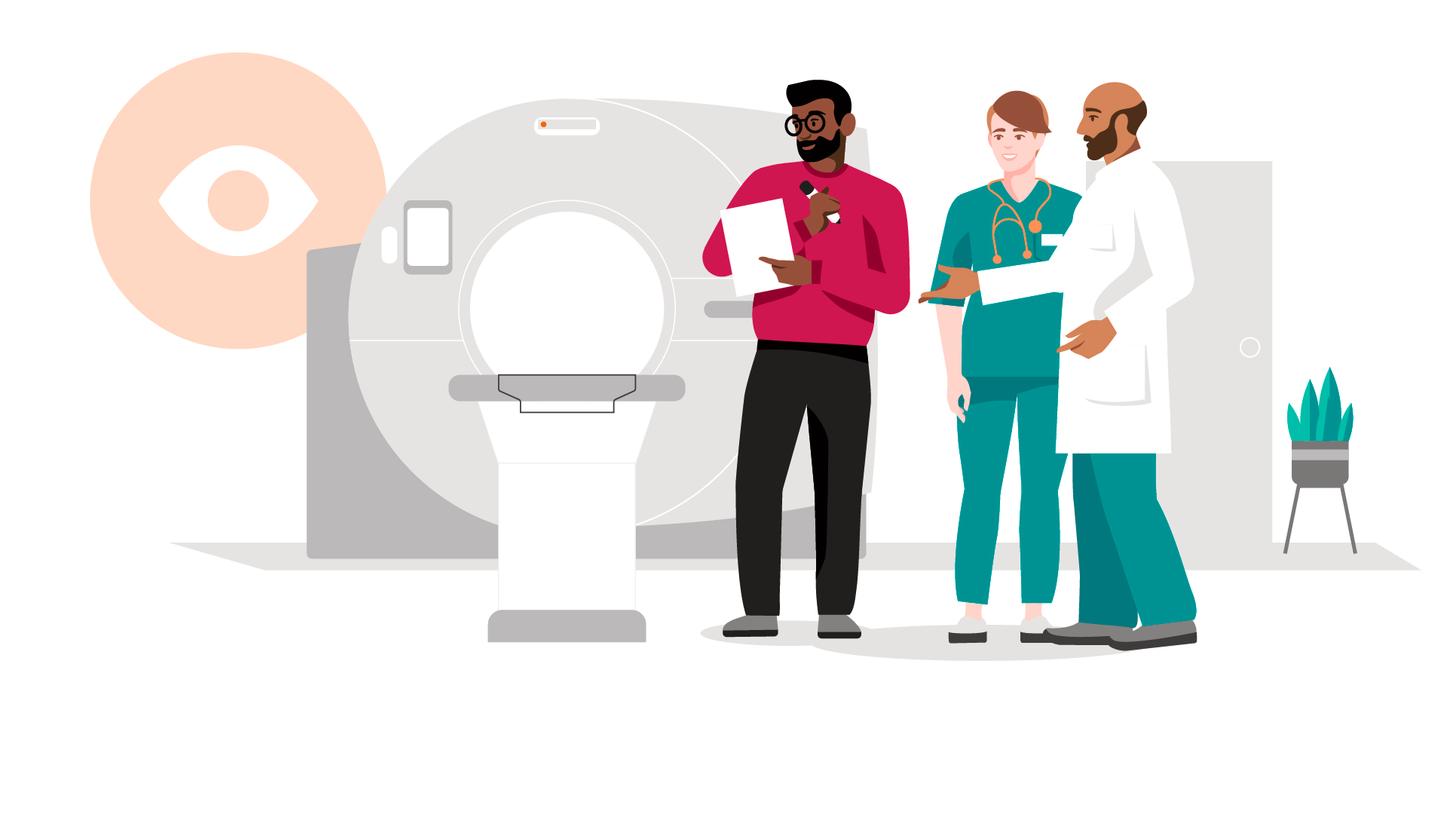
The UX Team then conducts in-depth research, observational analyses, and surveys targeting users and customers to find out exactly what they need.
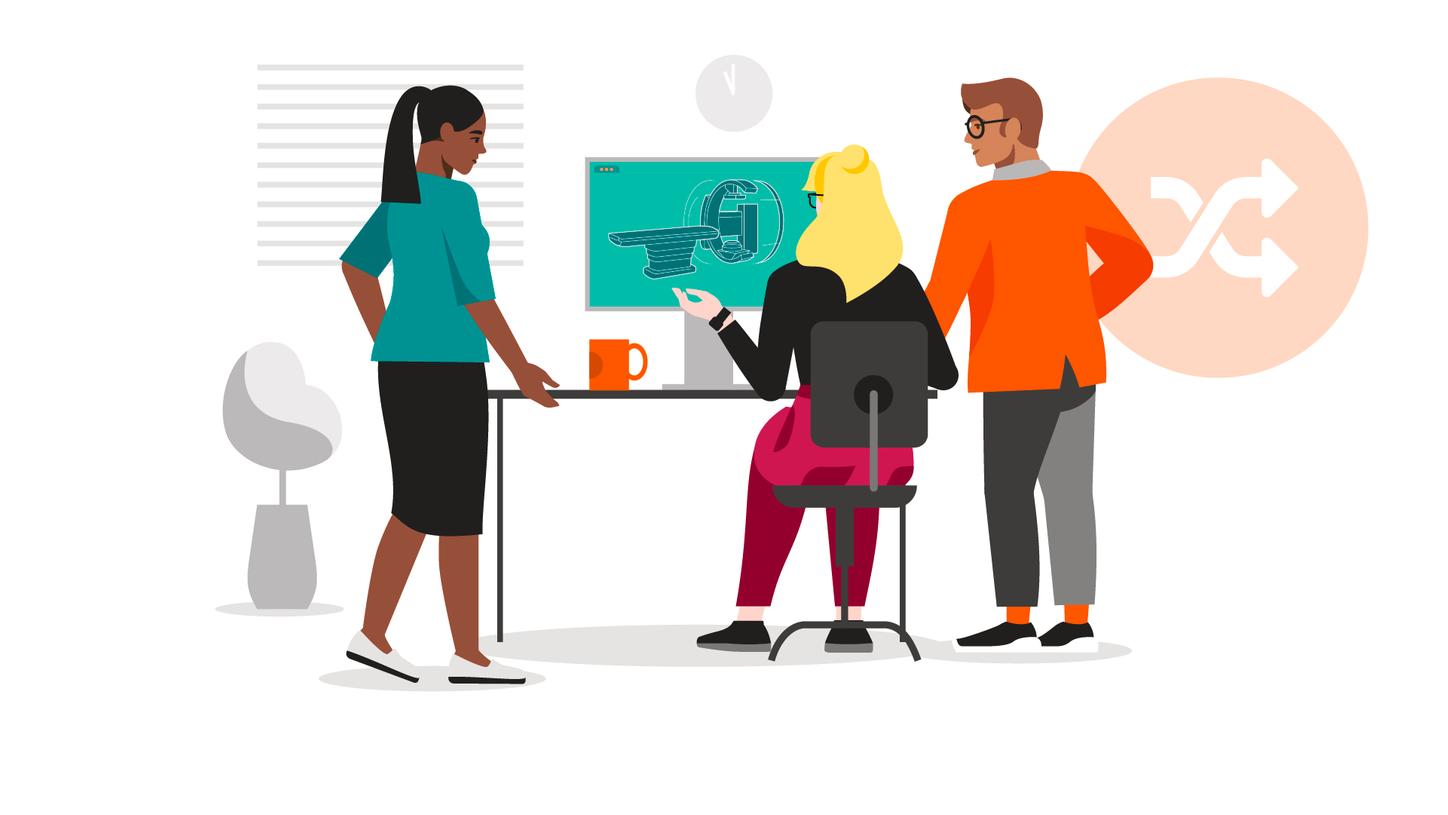
The team evaluates the insights they've gained to acquire the deepest possible understanding of the subject matter, and combines this knowledge with the technical requirements.
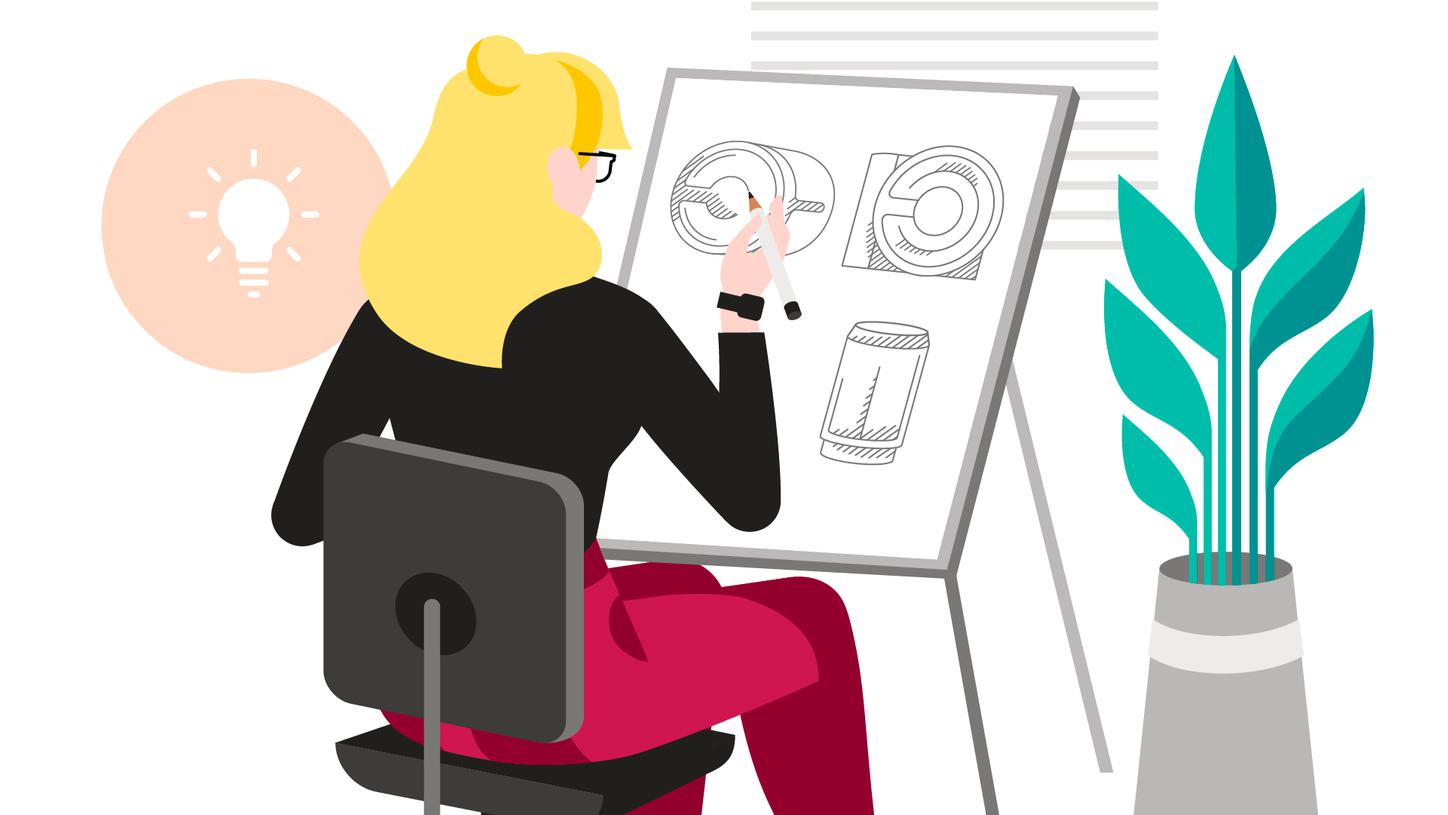
They then draft initial, simple sketches and visualizations of the product's design.
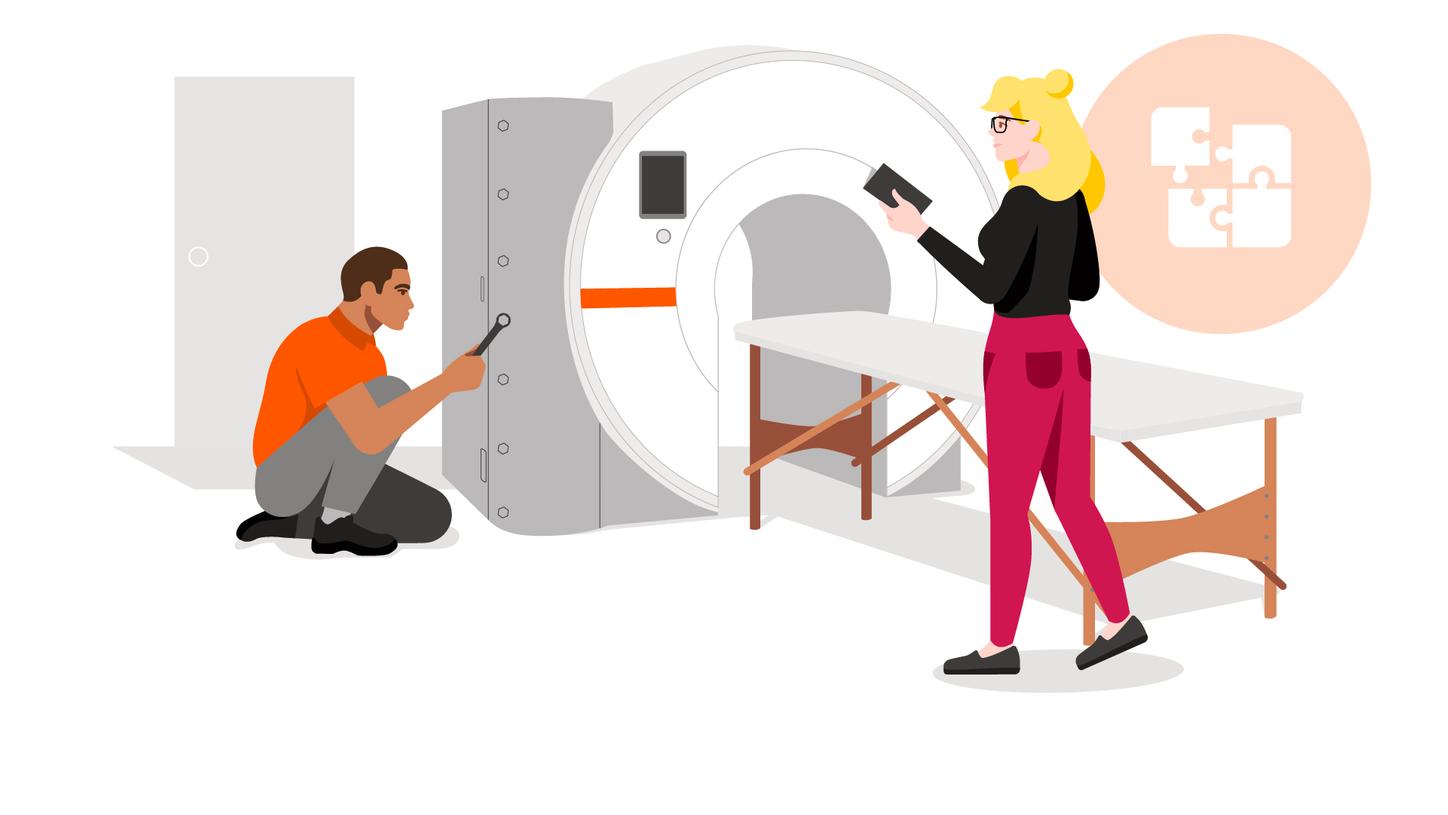
Next, the team constructs design prototypes of the product, right through to full-size models called mockups.
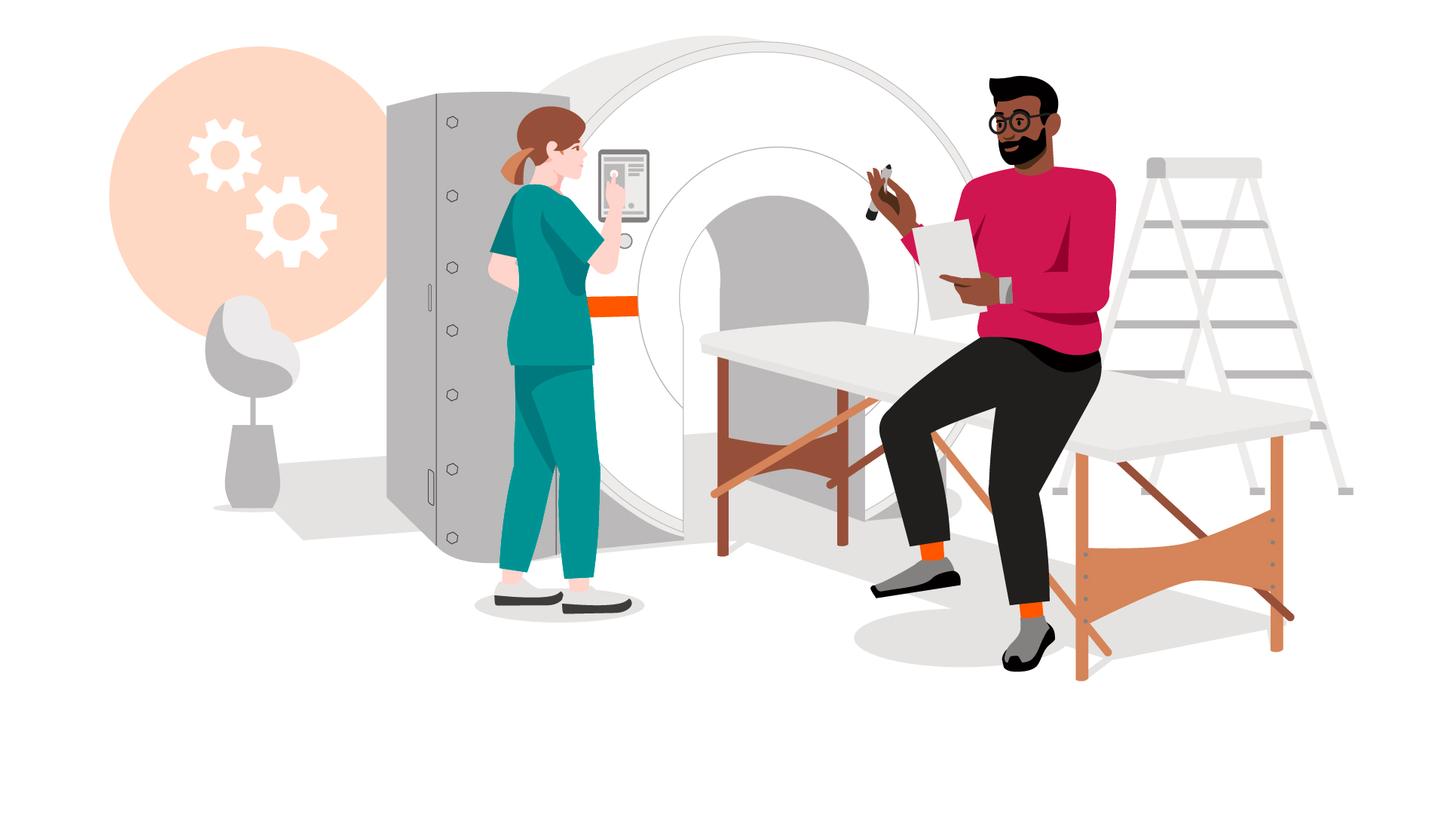
These prototypes undergo extensive test scenarios. Users deliver feedback on the product design's ease-of-use.
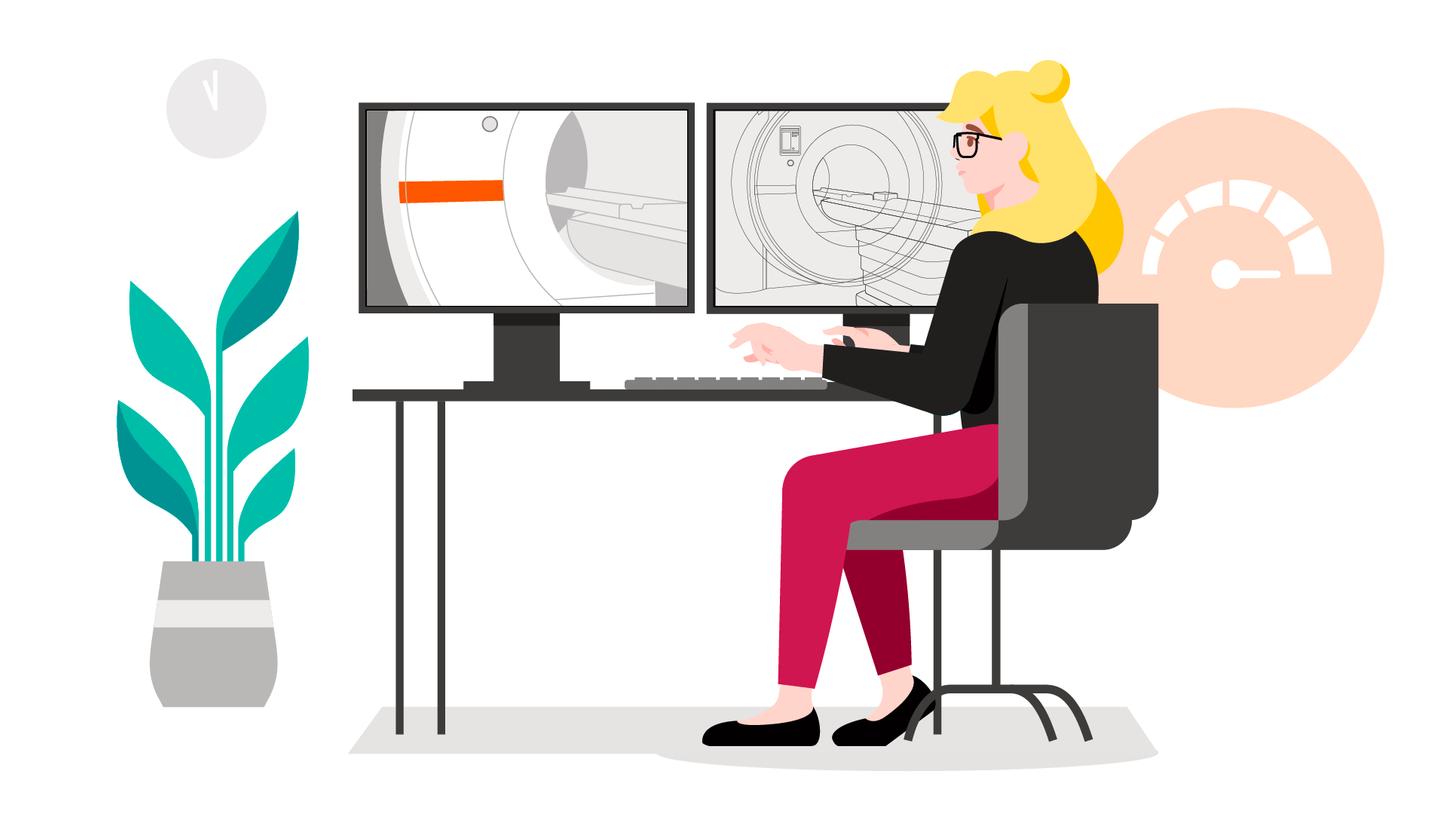
The team continues to improve the design based on these test results and the feedback received, and the visualizations become steadily more detailed.
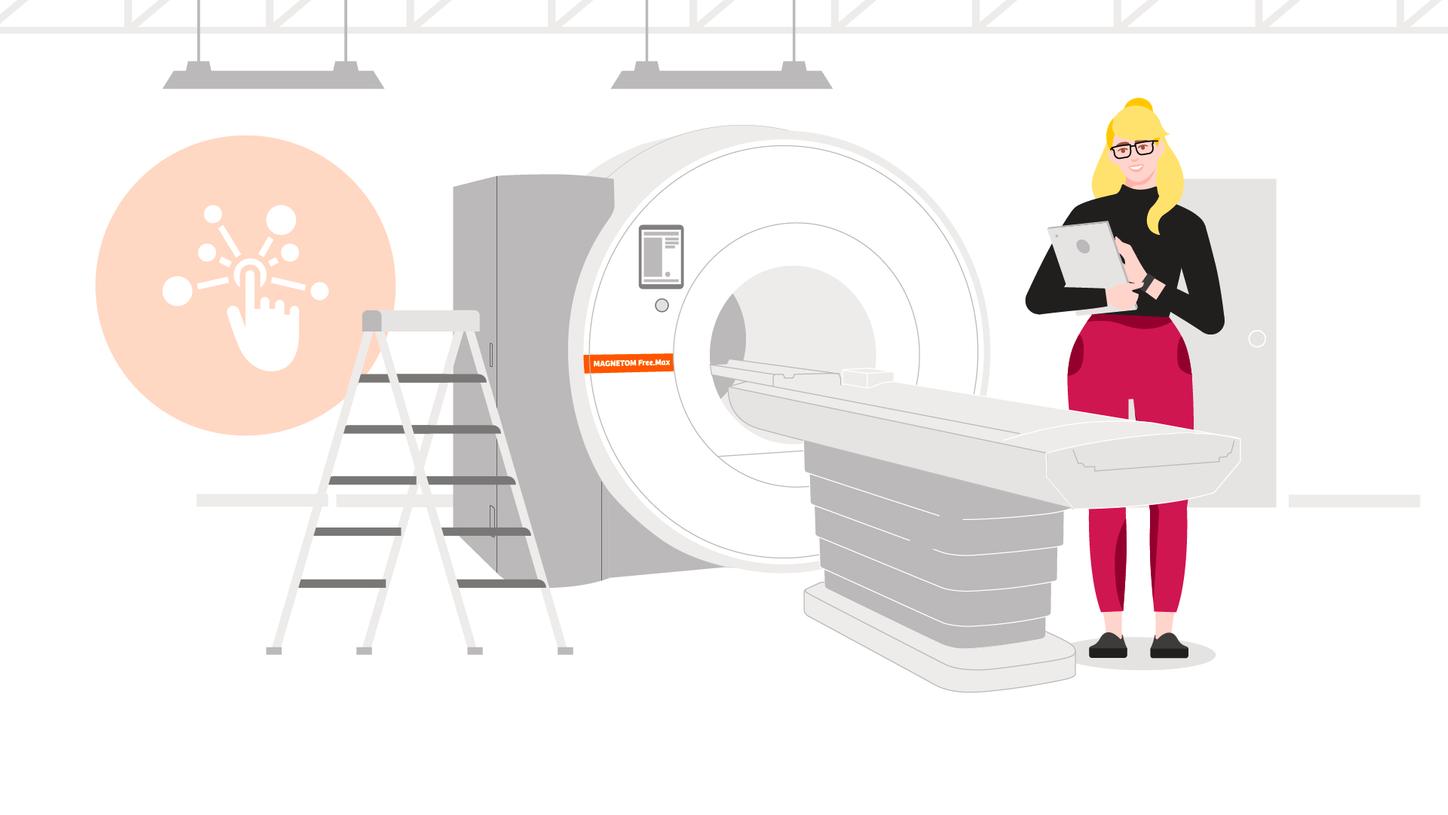
The product's design aspects and technical components are finally brought together, tested and finalized in the production plants.
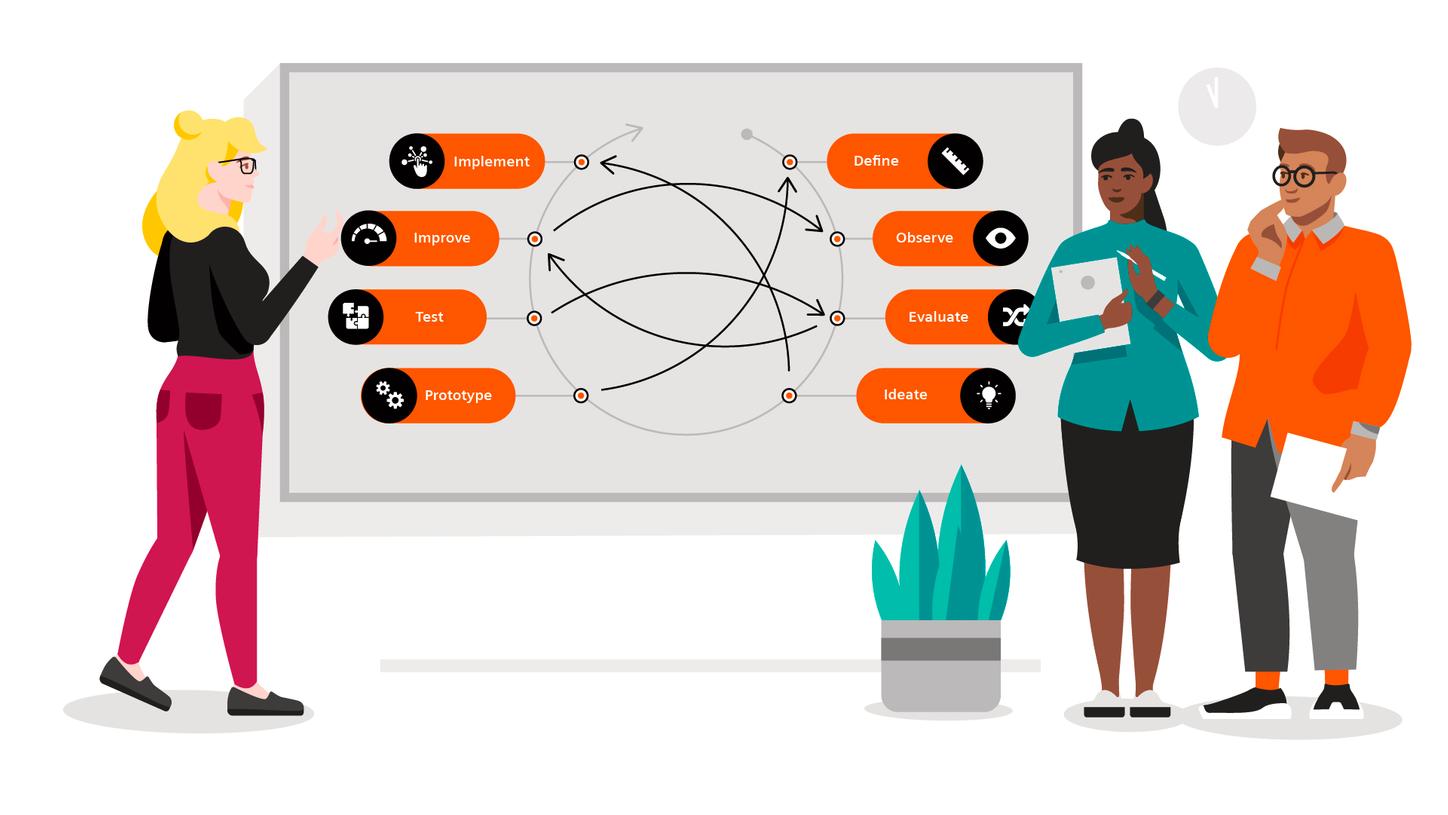
The team can repeat prior process steps at any time, depending what will best optimize the product design in each case.
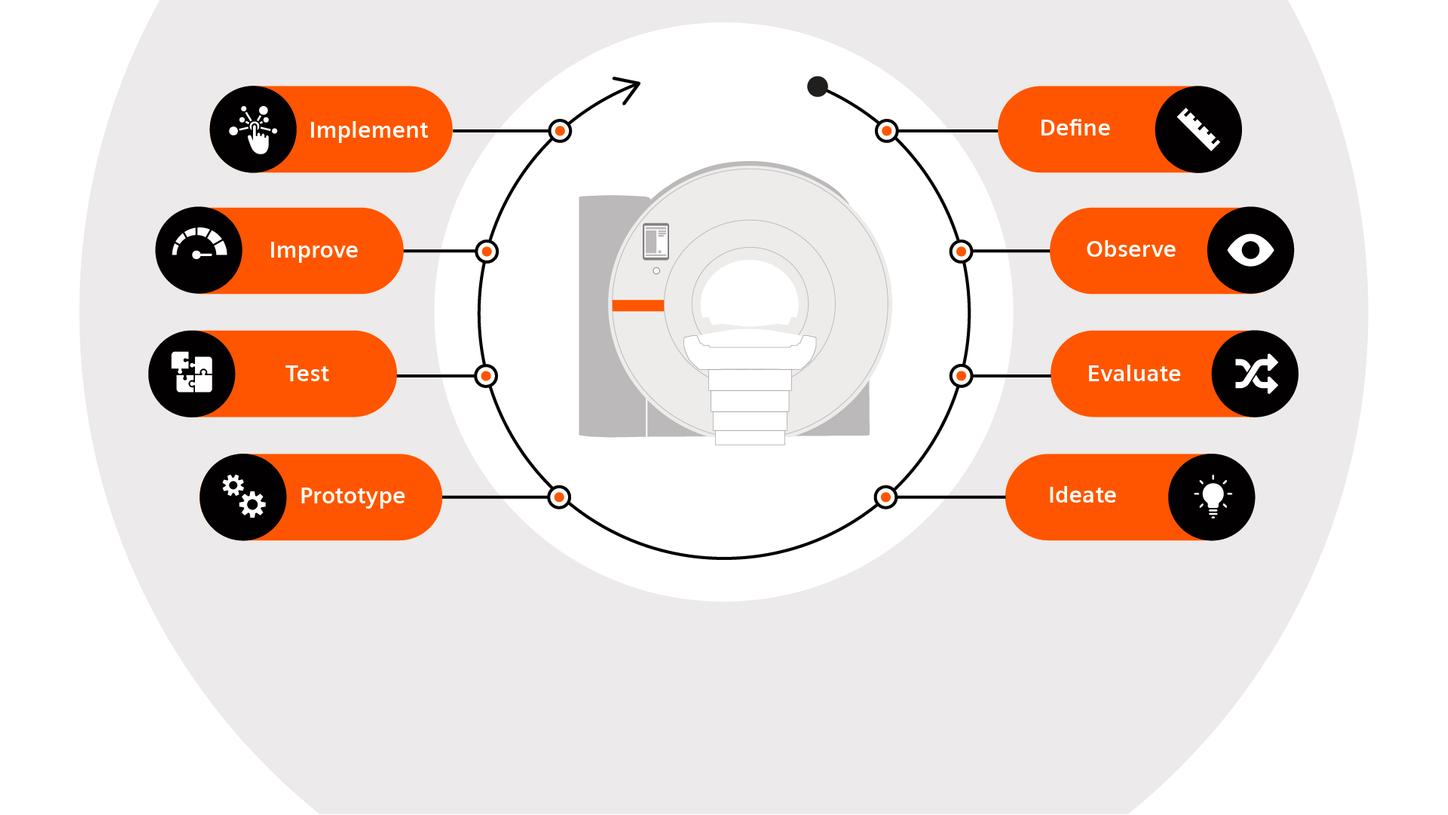
Extensive preliminary considerations, modeling, and testing are needed before products take on their final appearance. Everything is based on the "design thinking" approach.
Throughout the development process, Stefanie and her colleagues collaborate closely with the patent lawyers in the Intellectual Property Department to protect their designs internationally against plagiarism. Unlike invention patents covering technical developments, a design right legally protects aesthetic aspects. Protection covers not only the shape of a device, but also the complete detailed design in terms of form and color. Siemens Healthineers holds over 1,600 such designs rights worldwide.
In terms of their visual design, every product from Siemens Healthineers is to some extent unique. Yet, a specified core design system is of course also in place for product design, geared to create a distinctive, unmistakable look that stands for the brand values. This overarching design system at Siemens Healthineers is called "Shui". Stefanie helped to draw up the industrial design specifications for this system:
Under Section 1 of the German Act on the Legal Protection of Designs (DesignG), design means:
Quelle:
https://www.gesetze-im-internet.de/englisch_geschmmg/englisch_geschmmg.html#p0016
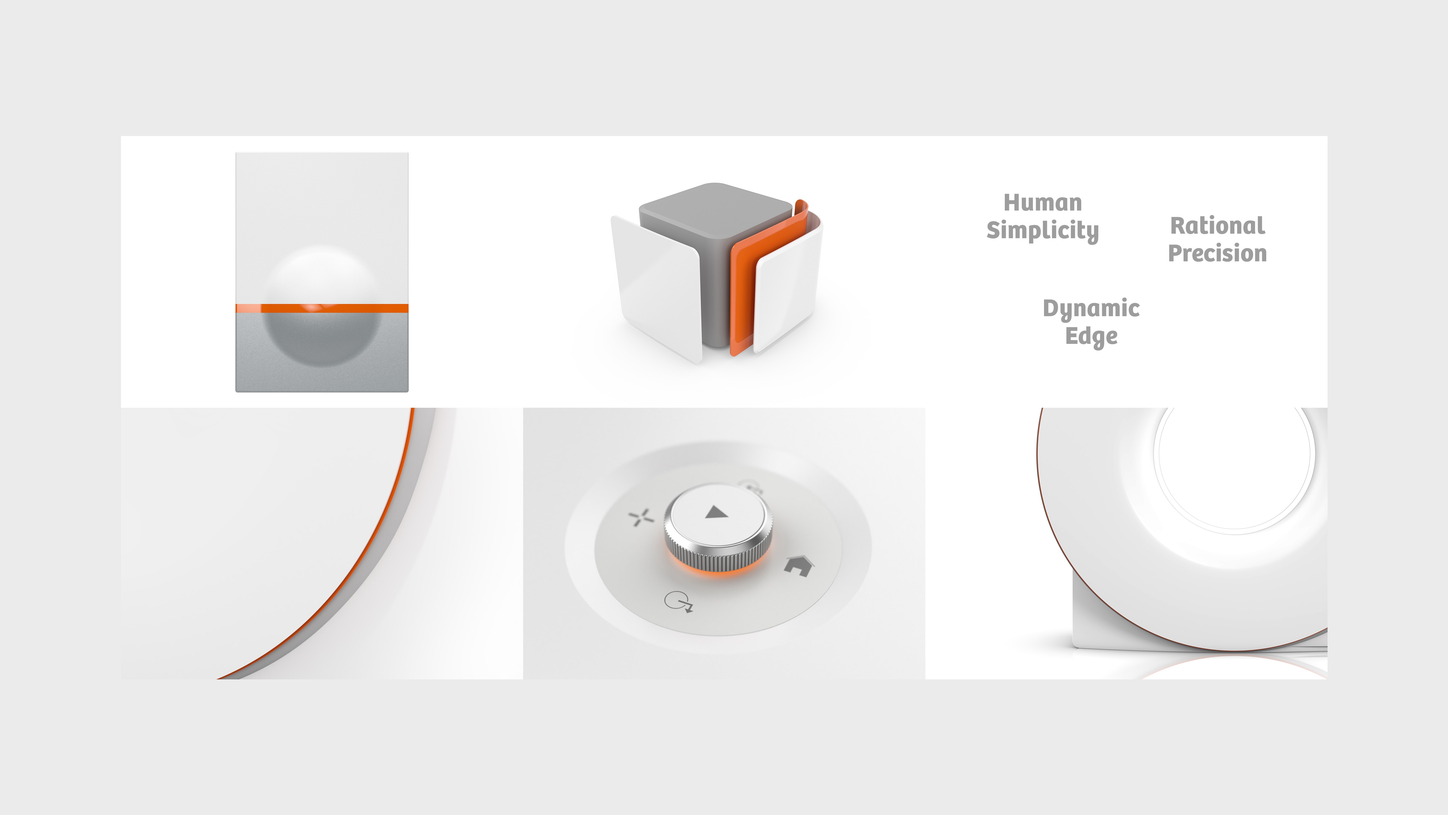
Stefanie co-developed the color and form language of our products in collaboration with her team colleagues. This language is backed by a sophisticated concept:
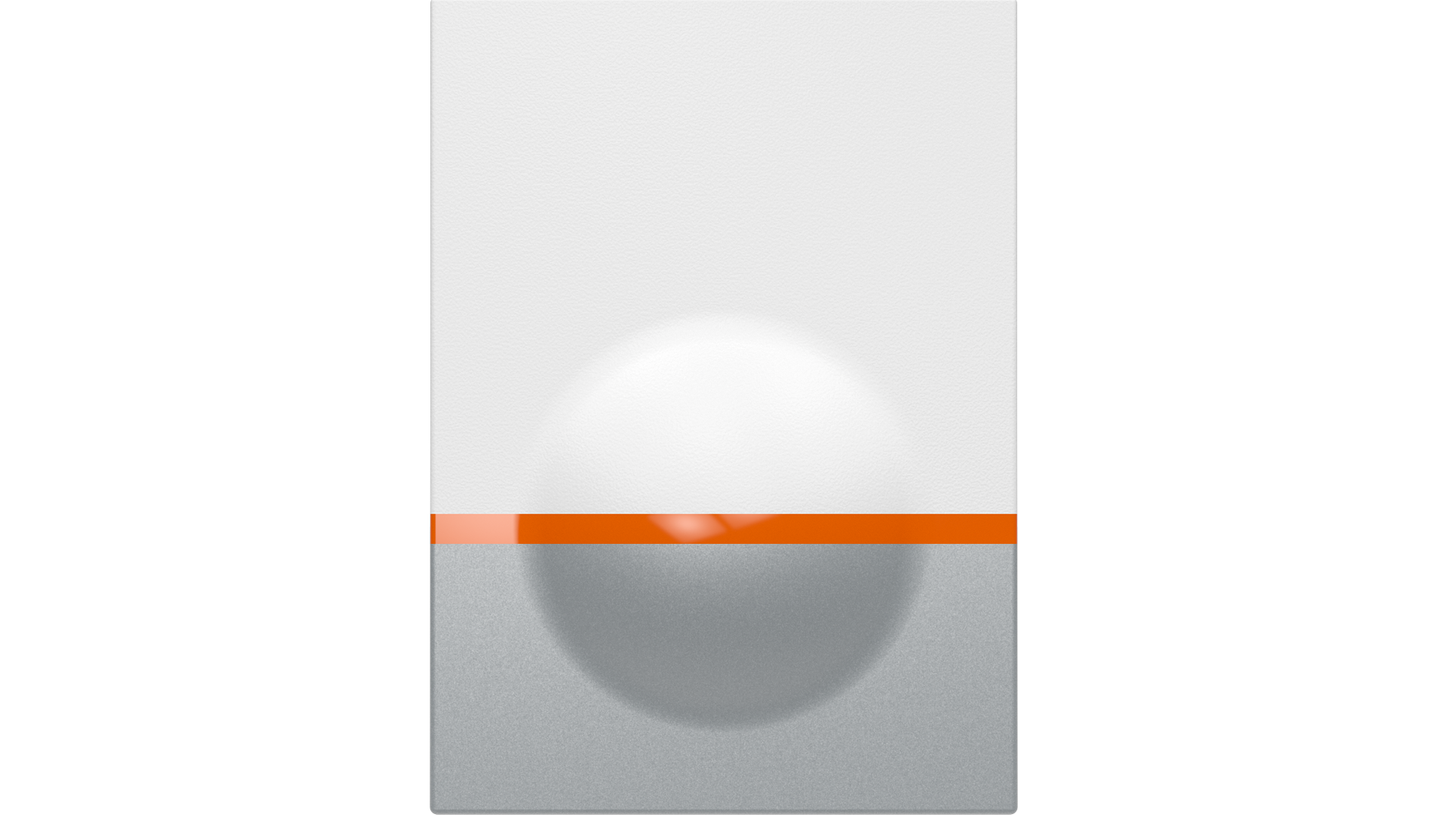
The three colors Signal White, Healthy Orange, and Aero Silver (or Aero Gray) together make up the uniform color scheme of all Siemens Healthineers products.
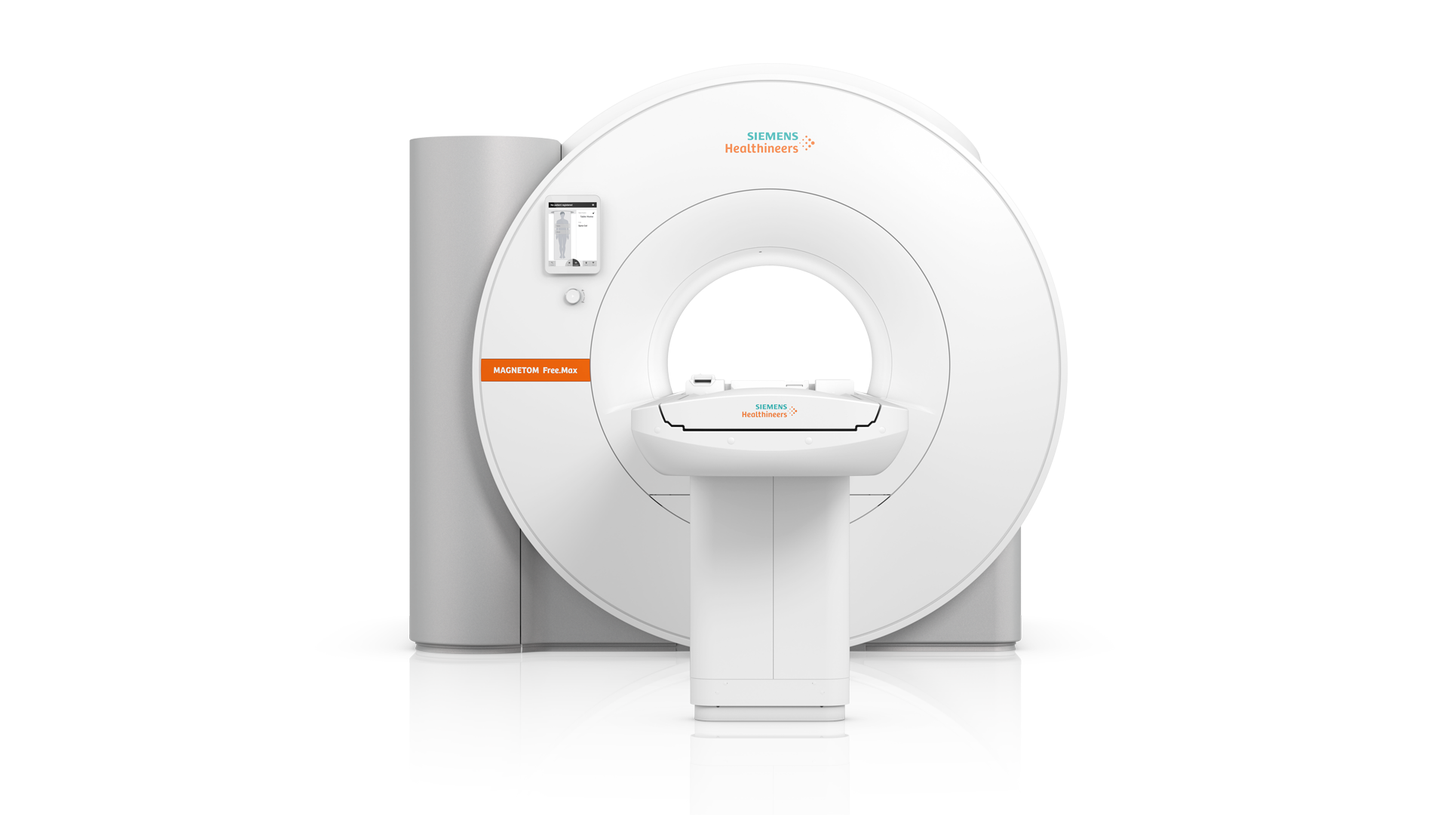
White lends a light and elegant effect as a primary color. Gray stands for technological reliability, and orange for the connectivity of our products.
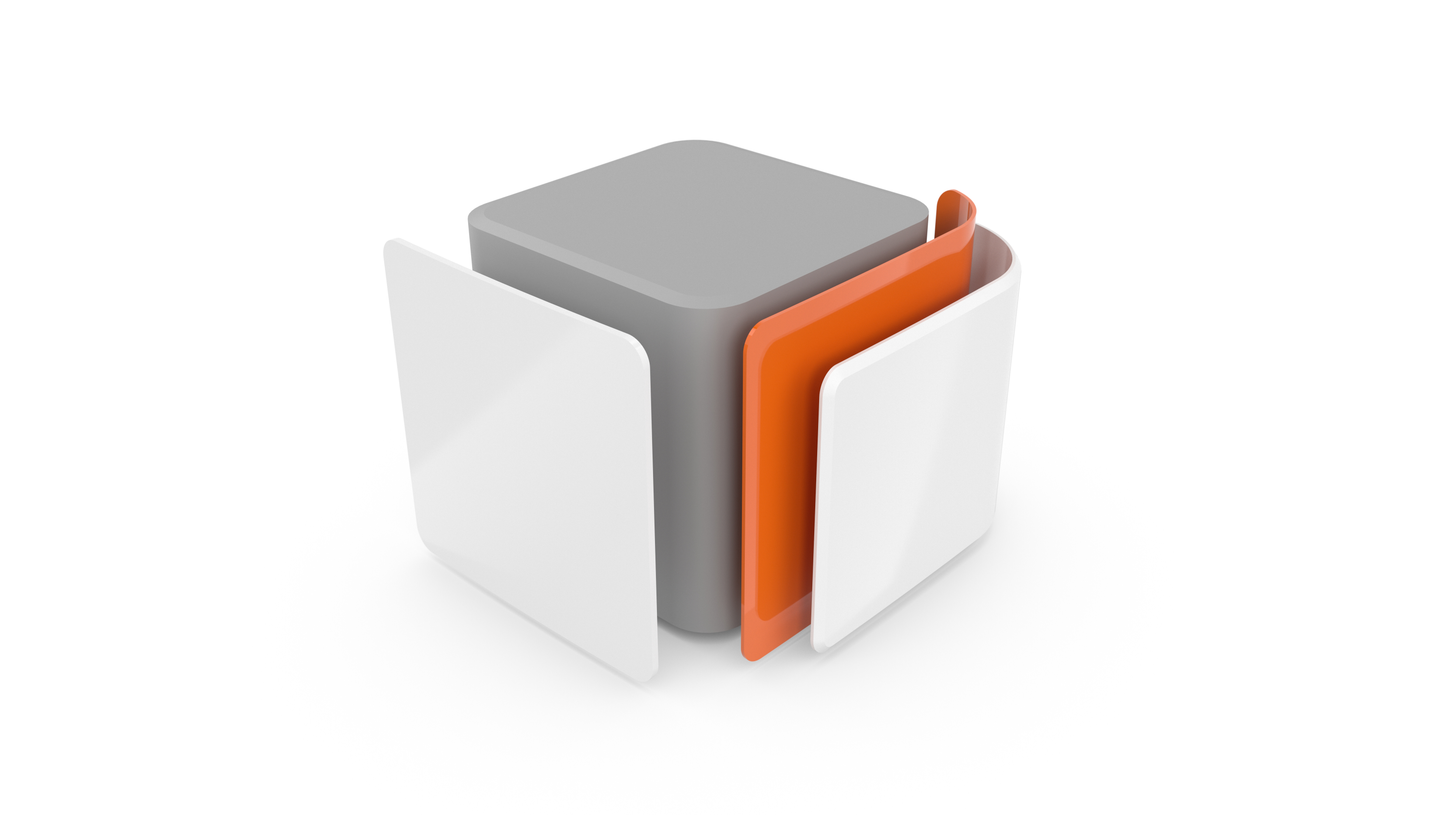
The design consists of three layer elements: The white shell encloses everything – harmonious and comforting. The gray core holds the technical elements.
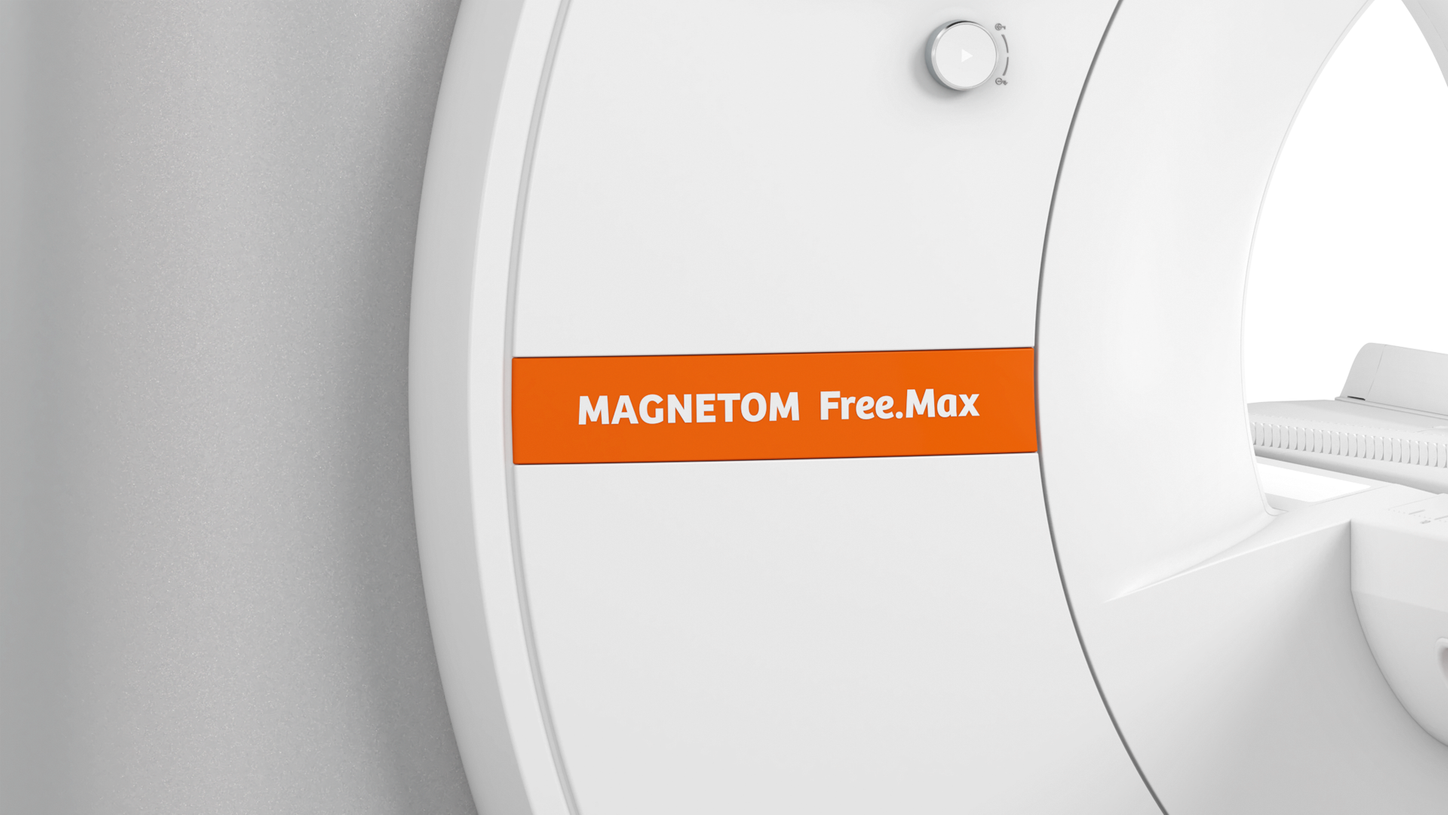
The horizontal, orange-colored stage creates a bond between the "technical" (gray) and "emotional" (white) levels. It bears the product name.
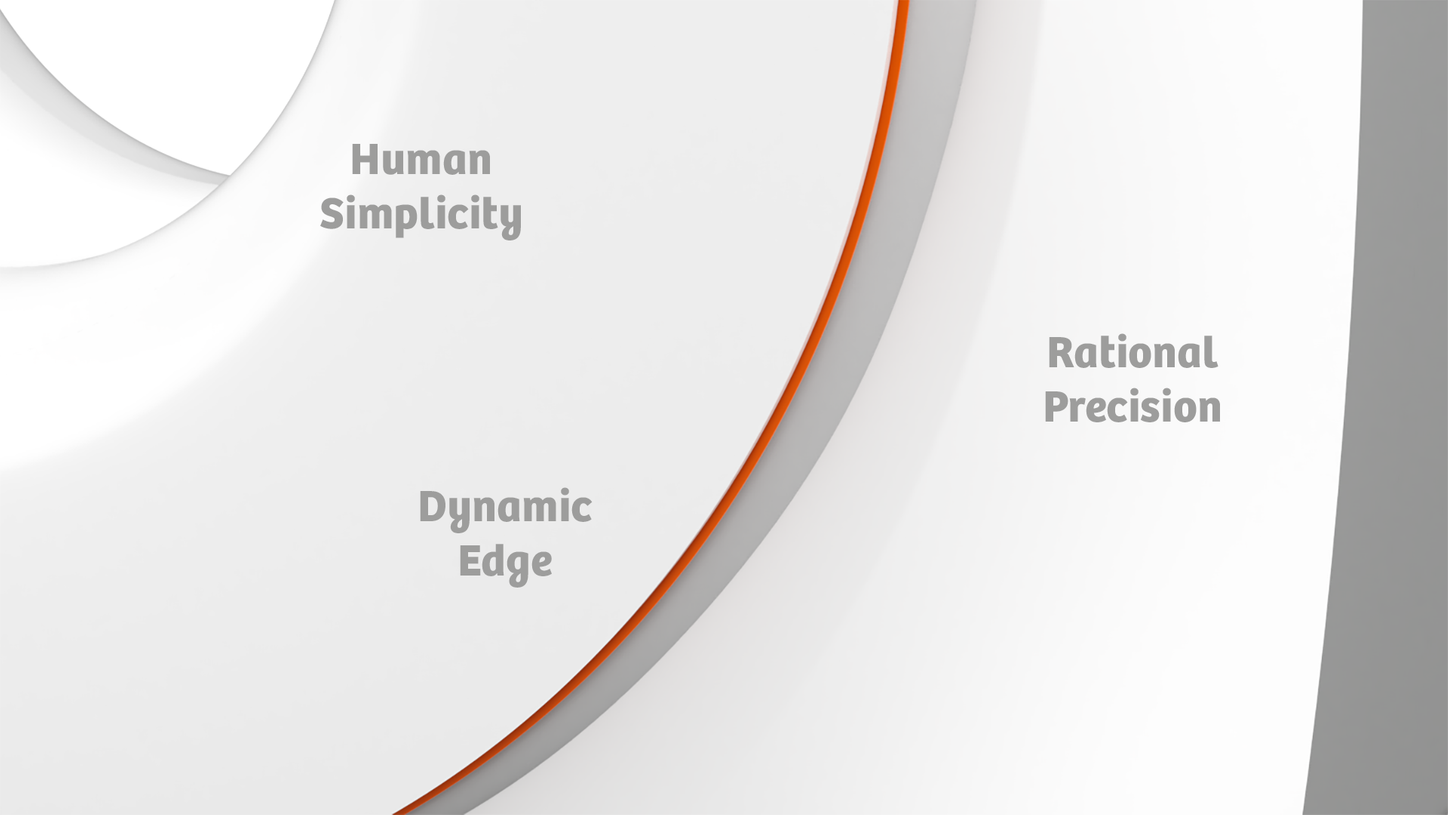
Reduced design styles stand for the authenticity and approachability of our brand. Geometric shapes and rounded-off edges communicate a sense of comfort.
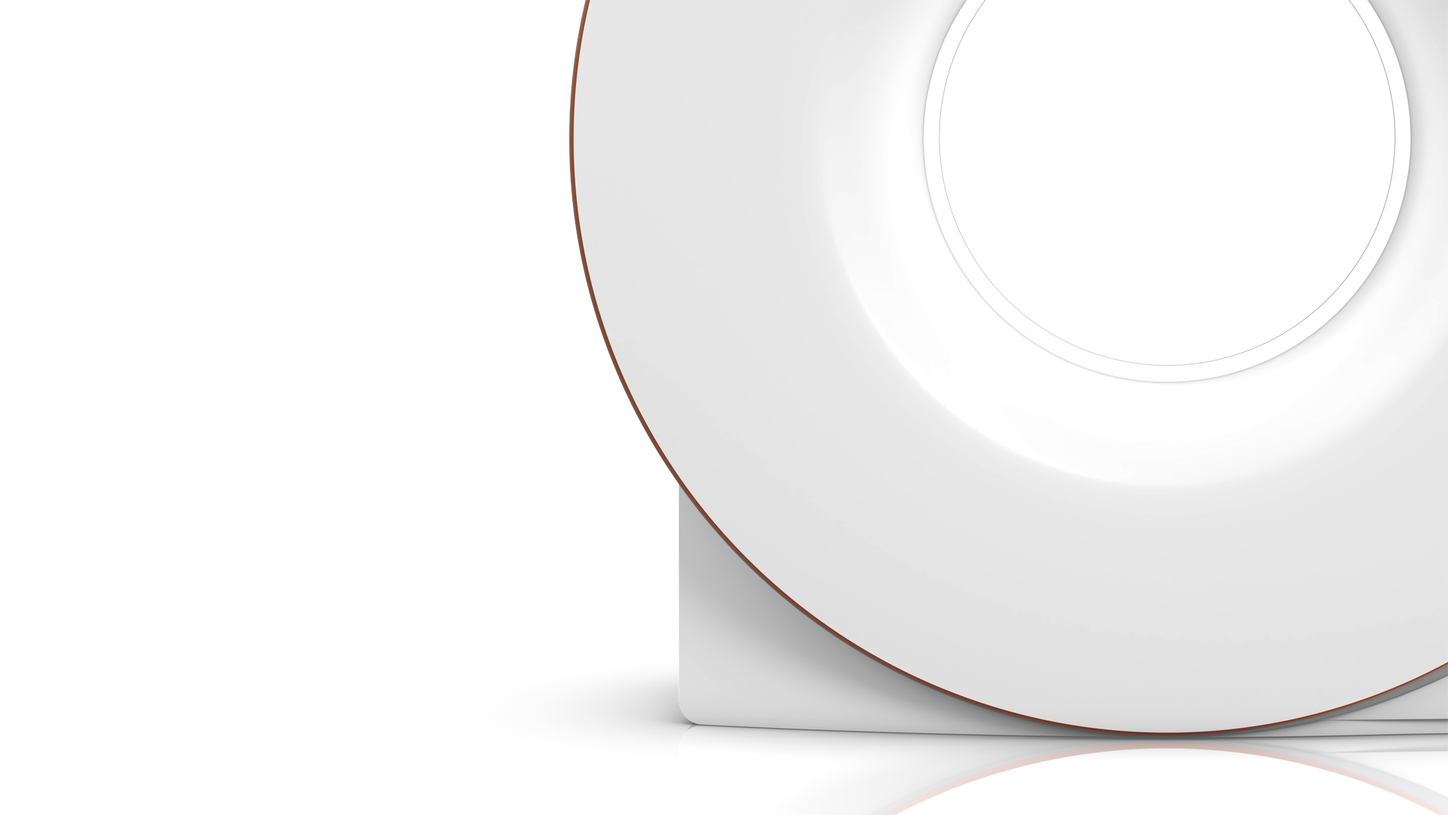
This design feature shapes the overall visual character: it stands for safety, tradition, care, and a people-centric approach.
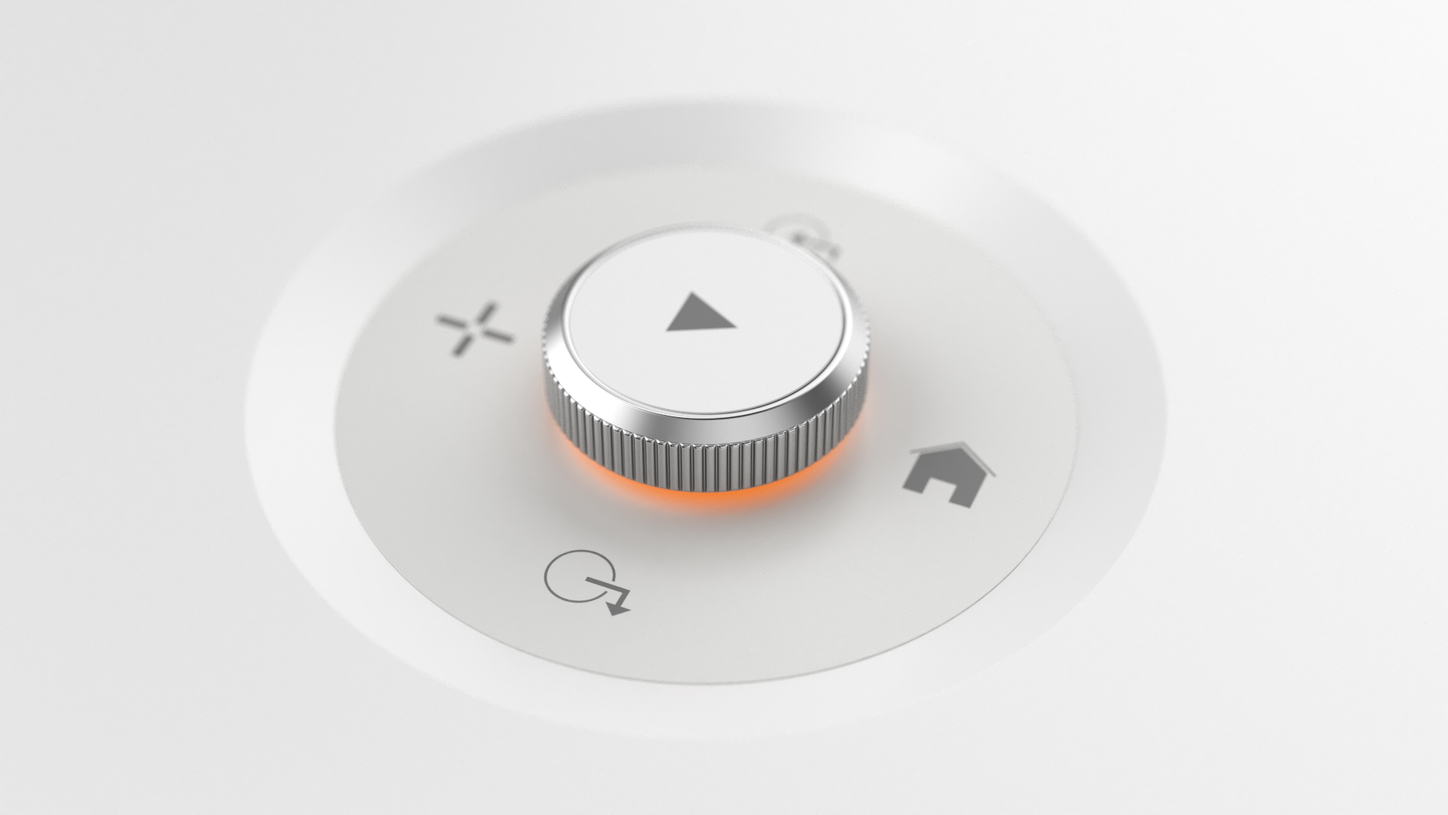
This guideline creates a strong sense of trust and confidence – in the technical control of the product as well. It stands for the values of ergonomics, precision, and quality.
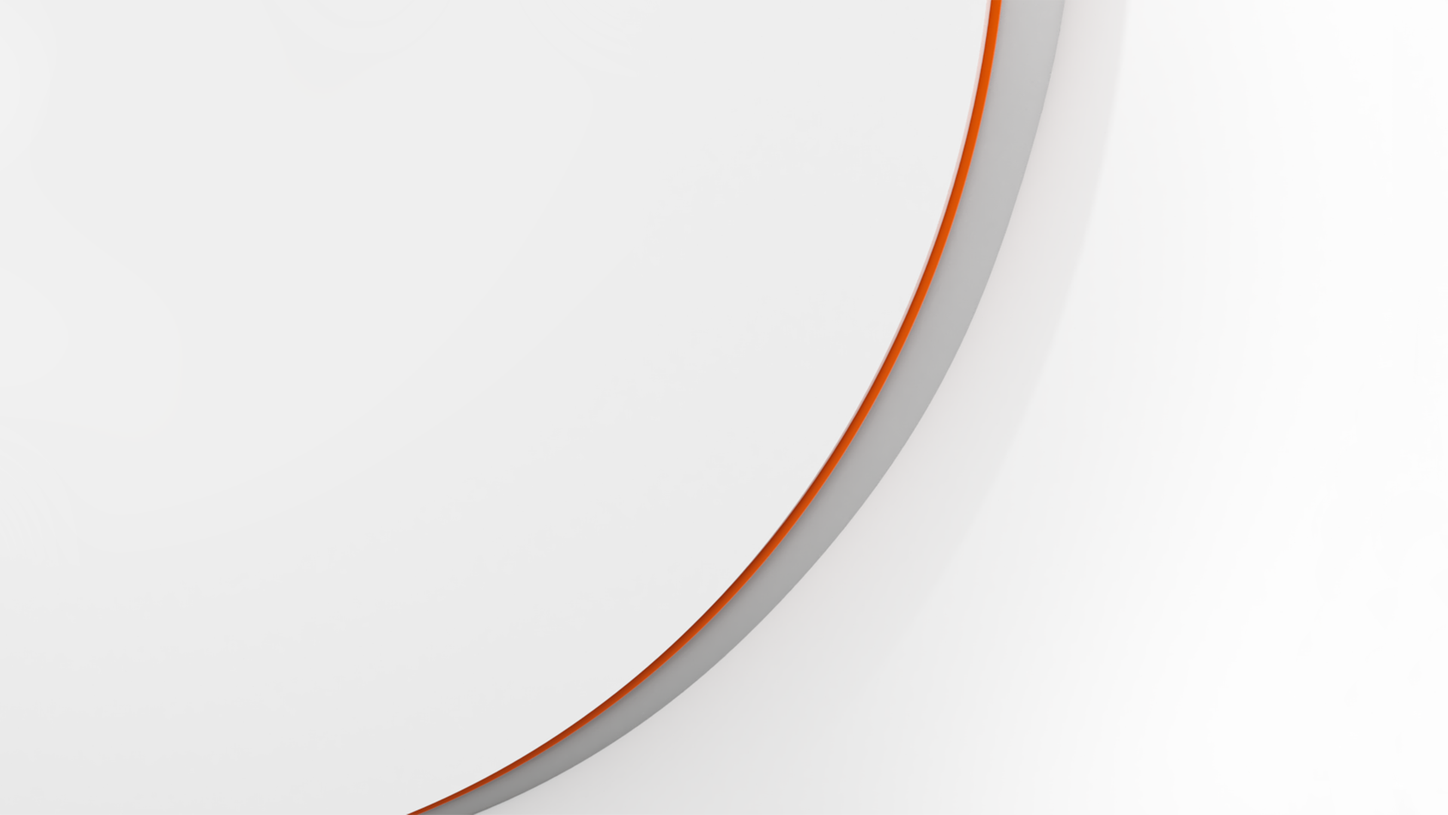
This principle creates an inspiring, dynamic design language. It communicates the values of innovation, technological advancement, and a pioneering role.
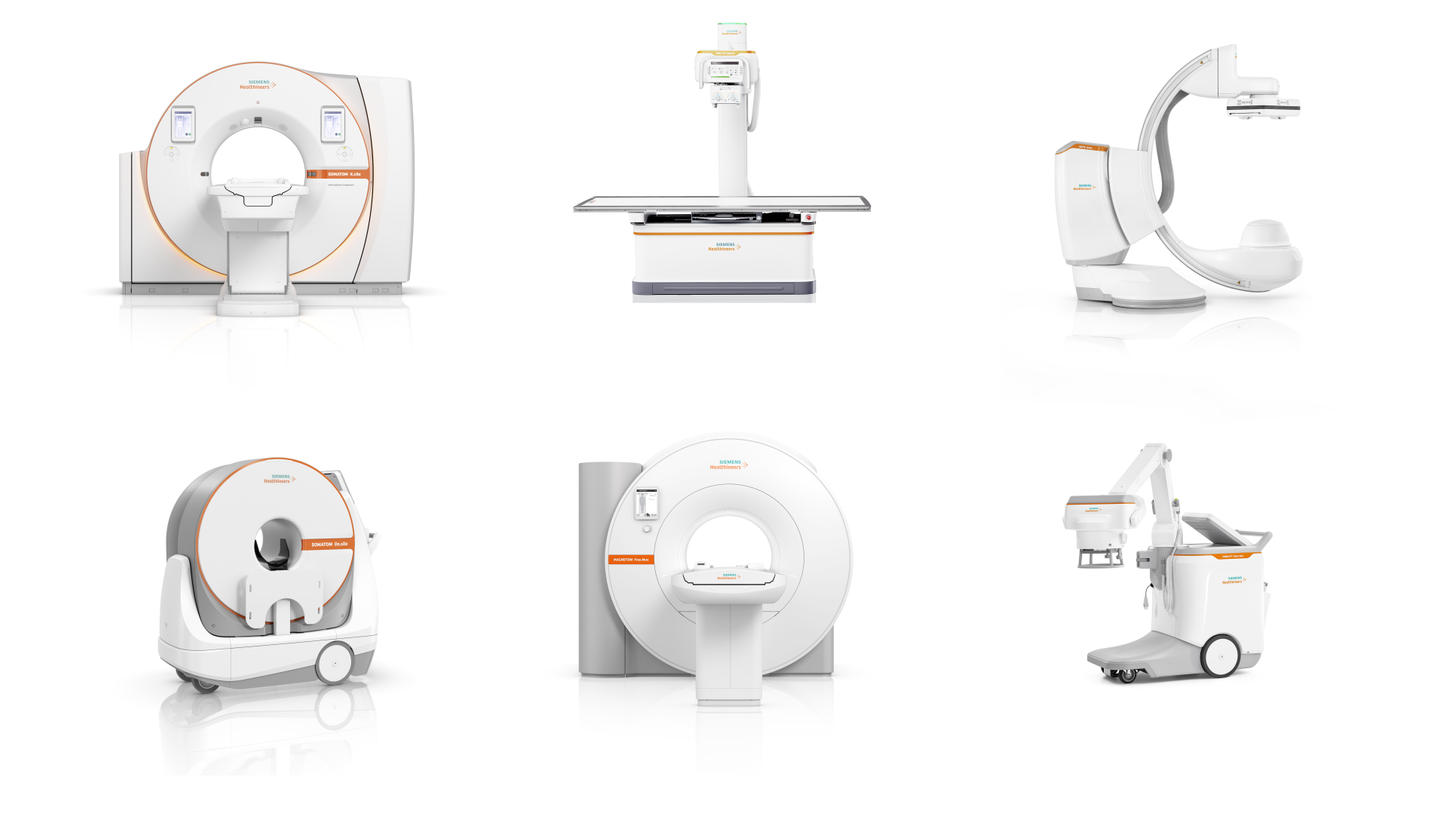
This uniform product language – expressed by incisive colors and distinctive forms – lends all of our products their unique, unmistakable "face".
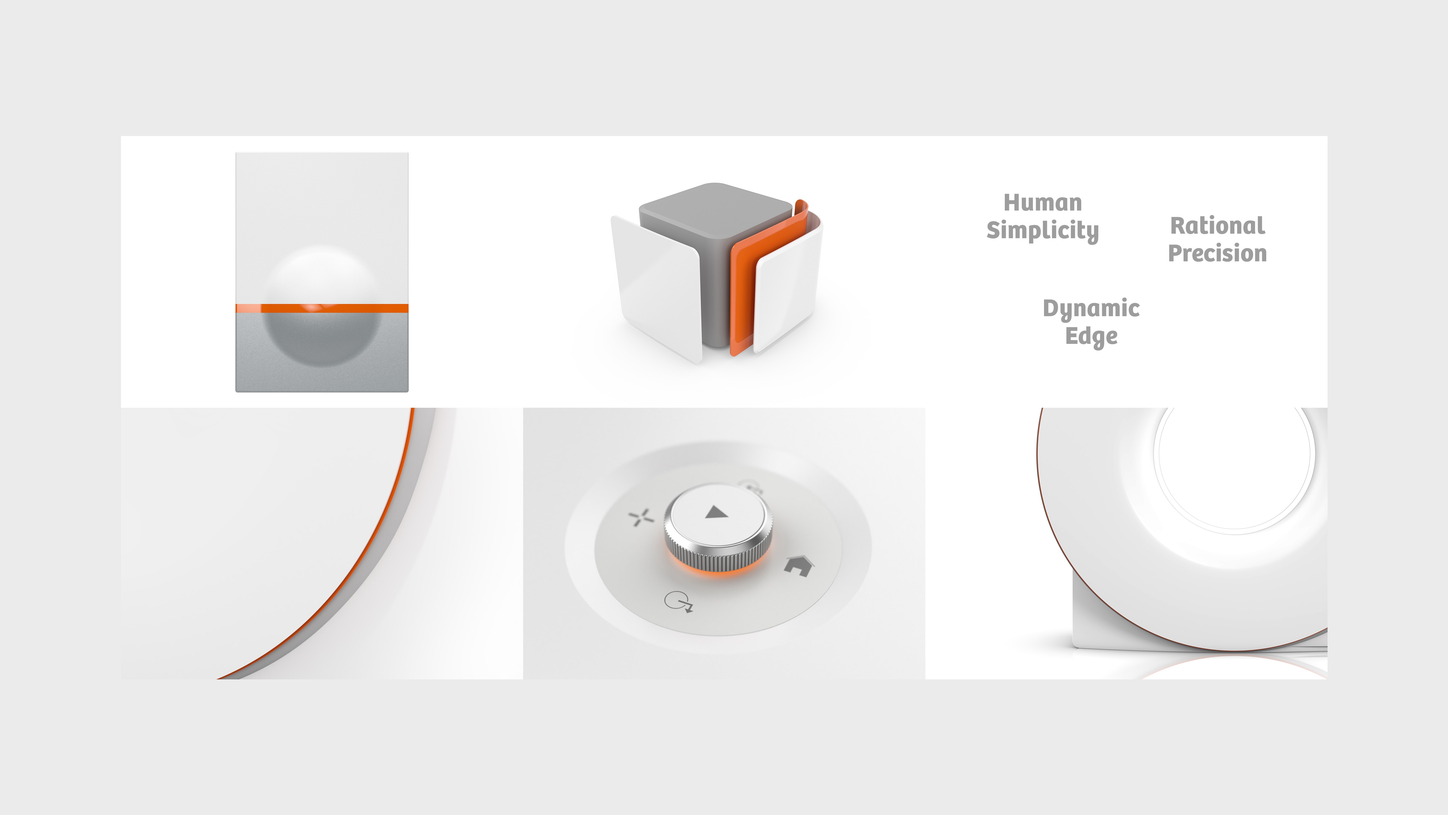
Stefanie co-developed the color and form language of our products in collaboration with her team colleagues. This language is backed by a sophisticated concept:
The Industrial Design Team has won several different awards for its work. For its design of the MAGNETOM Free.Max magnetic resonance scanner, the team took home the Red Dot Design Award in 2021. Stefanie was the design lead responsible for the result.
Red Dot Design Award
The Red Dot Design Award is an international design competition for product design.
“Red Dot” winner
MAGNETOM Free.Max
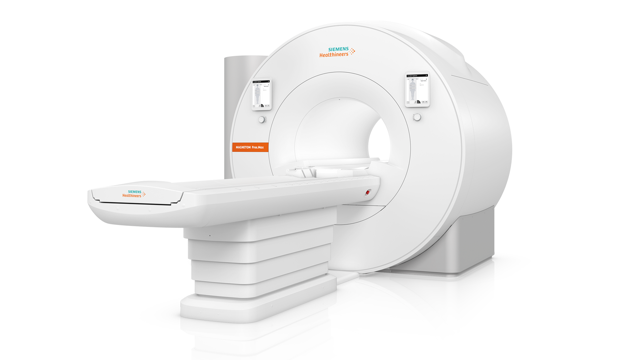
The statement by the jury reads: "The MAGNETOM Free.Max surprises people with its unusual dimensions and masterfully puristic design."
Two key product advantages of the MAGNETOM Free.Max are decisively related not just to the innovation in its technical form, but also to its design: the scanner's transport height, and the diameter of the patient bore. "In the past, hospital walls sometimes had to be torn down to get an MRI scanner into the building," Stefanie explains. With a transport height of less than two meters, the MAGNETOM Free.Max easily fits through normal doorways.
Making patient examinations more comfortable
Another exceptional feature is the large patient bore, with a diameter of 80 centimeters – the widest of any whole-body MRI scanner ever built. This puts patients who are anxious, claustrophobic, or very corpulent at greater ease, allowing more comfortable examinations.
What is the standard diameter of a MRI scanner bore?
The success of the team has always been the most important thing for her, says Stefanie. When she finally stands in front of a finished product after such a long development period, it fills her with pride: "And if on top of everything else, we also win an award, that's of course fantastic."
Join the team Siemens Healthineers
Are you also interested in joining our passionate team?
More a calling than a profession
Does the profession of product designer affect her private life in any way? "You obviously look at everyday products through different eyes. Whether it's architecture, fashion or cars: everything has its own design, sometimes better, sometimes not so good. There's a saying that designing isn't actually a profession, but a calling. So, in your private life, you can't of course switch off completely." Stefanie admits with a laugh that, when building her own home, she even shadow-mapped her terrace by computer simulation in a 3D program: "What angle will the sun shine at, how much shade is needed…" True makers don't leave anything to chance.
Share this page
Katja Gäbelein works as an editor in corporate communications at Siemens Healthineers, and specializes in technology and innovation topics. She writes for text and film media.
Assistant editor: Guadalupe Sanchez