Home
Perspectives
- Indispensable in MedTech
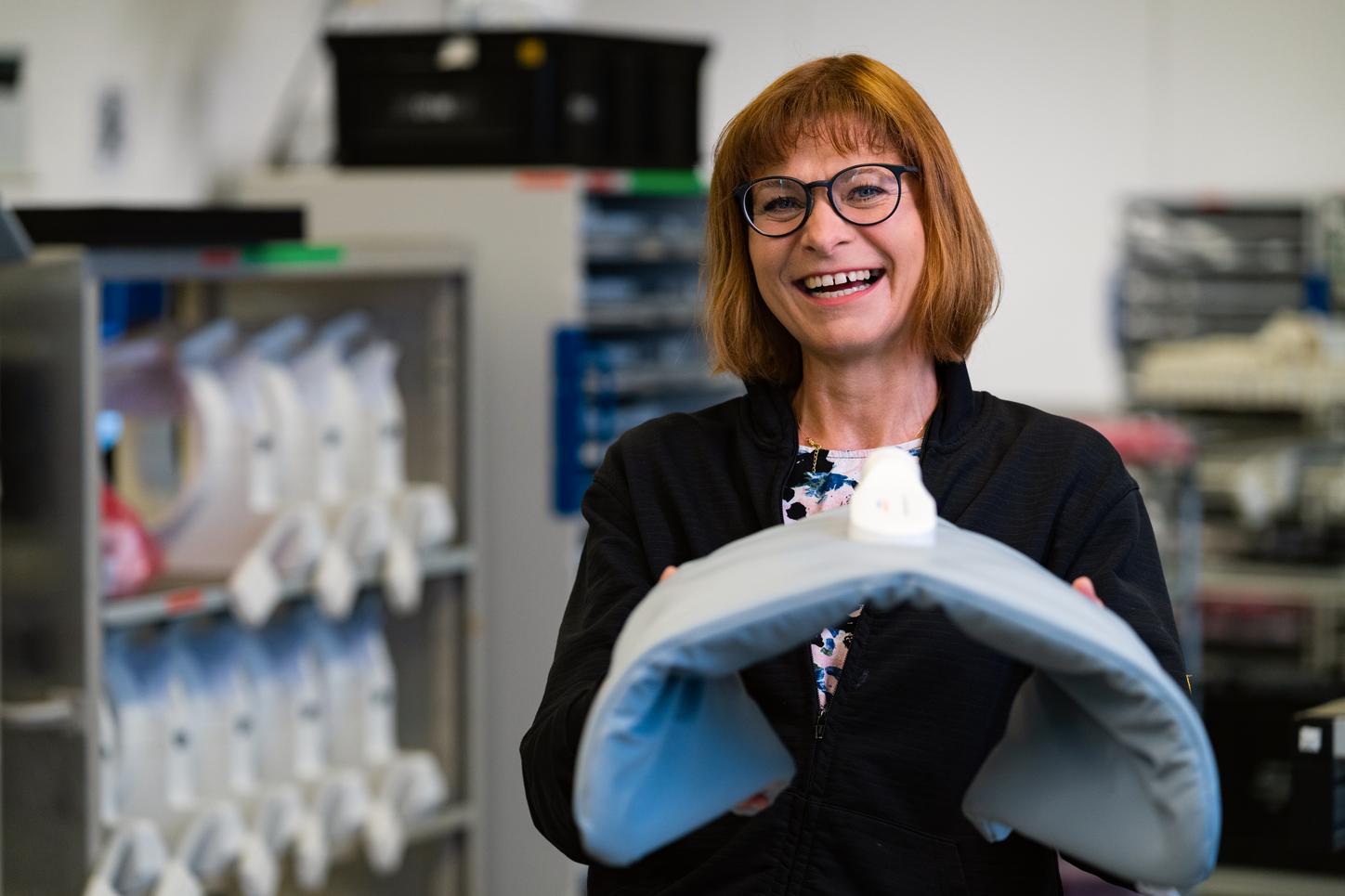
Imaging
Indispensable in MedTech
How plastic makes the world go round in medical technology
6min
Elena Kleffel
Published on September 7, 2022
Coils that come in contact with patients should be as soft as pillows, not as hard as tabletops – it is a puzzle that Yvonne Candidus is piecing together.
<p>Anybody who has ever had an MRI scan knows one fact of life quite well: It amounts to a very close encounter with lots and lots of plastic. This dependency on plastic hardly stops with the bore of the MRI system and the local coils that may be placed around the part of the body that will be examined – an MRI system uses the widest variety of this material on many other places as well.</p><p>Yvonne Candidus, a college-educated materials scientist who has overseen the development of <a href="local%20coils">local coils</a> at Siemens Healthineers for 26 years, knows exactly why things are this way. For an MRI scan to be helpful, a coil must fit as perfectly as possible – while being just as comfortable.</p>
Local coils
Local coils are placed directly on the patient during the scan. With the help of antennas installed in them, the coils capture the signals of hydrogen atoms that are excited by the scanner’s magnets. Software is then used to turn the signals into images.
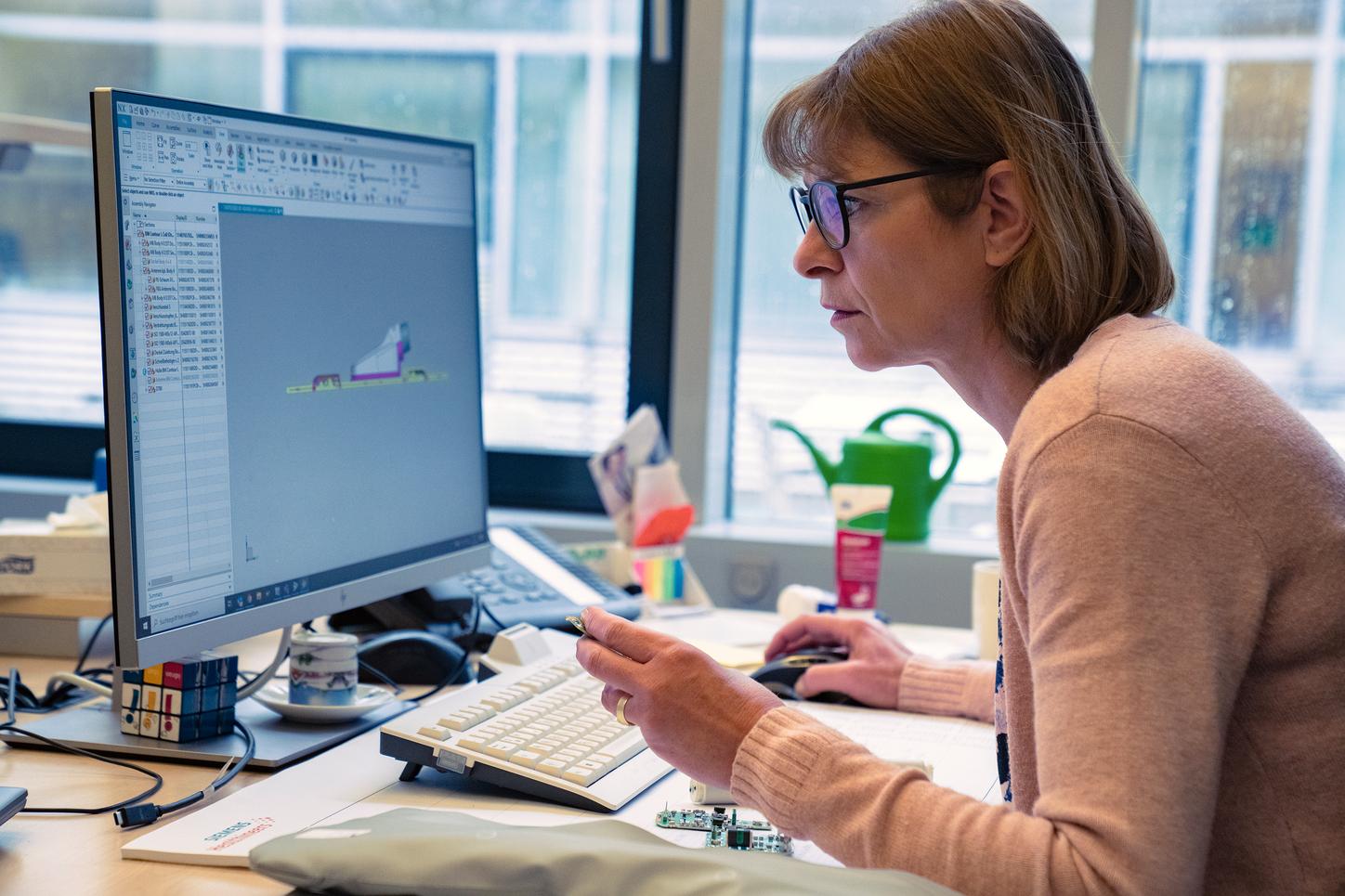
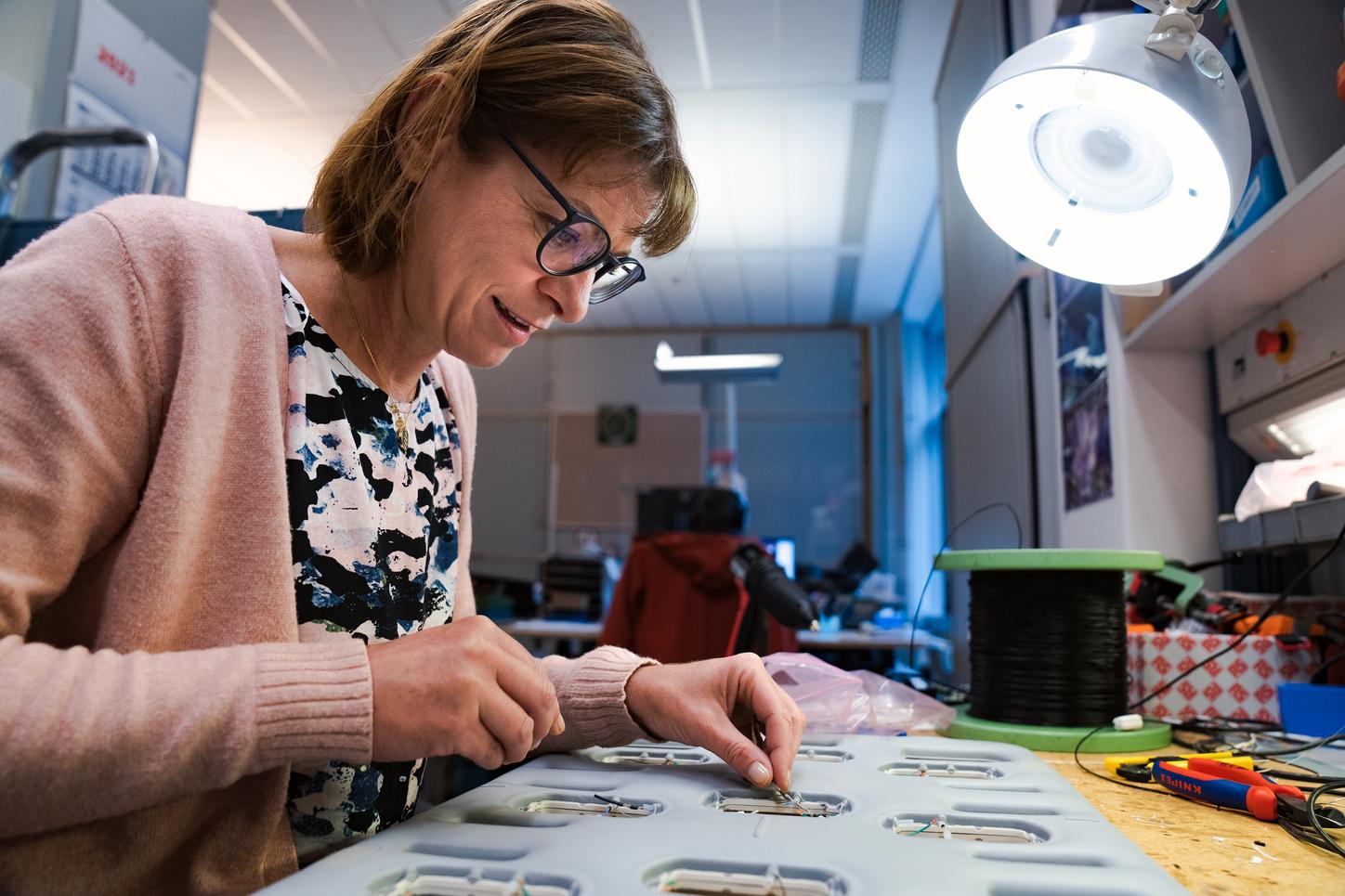
From rock-hard foam plastic to cozy pillows
<p>Years ago, local coils were relatively immovable pockets that contained antennas. No more. Today’s coils are flexible, an achievement made possible by ultrasound welding technology. The result is a small, very comfortable pillow. In the Magnetic Resonance Experience Center in Erlangen, the plastics expert has been presenting the results of work that her team and she have been conducting for months: a flexible local coil<sup>1</sup>. The plastic is indeed pliable.</p><p>The team started the journey that led to this innovation by initially weighing two questions: How flexible should the coil be? And how small could the antenna housing be made? They then consulted with the high frequency developers involved in the project. Afterward, they went about the task of coming up with the right mix of materials – a job in which they put their knowledge of plastics to the test. Plastic can have such a wide variety of characteristics: It can be hard, soft or lightweight. It can stand up to heat and radiation. And it is flexible to work with.</p><p>“Naturally, the most important requirement of all is that the material used in the local coil should be non-imaging,” Yvonne Candidus says. “This is another reason why plastic is frequently the material of choice in medical technology.”</p><p>Having made their selection, the team members then began to produce their first prototypes. “We almost always use 3D printers to do this job,” Candidus says. “Afterward, we conduct a range of tests with the prototypes.”</p><p>During this work, the team examines such questions as flammability or resistance to media or UV radiation. One particularly important question is whether the prototype is compatible with disinfectants and cleaning agents. “Plastics are all-rounders,” says Sebastian Köppl, the colleague from materials engineering who conducts the tests. “We can’t do without them in medical technology.”</p>
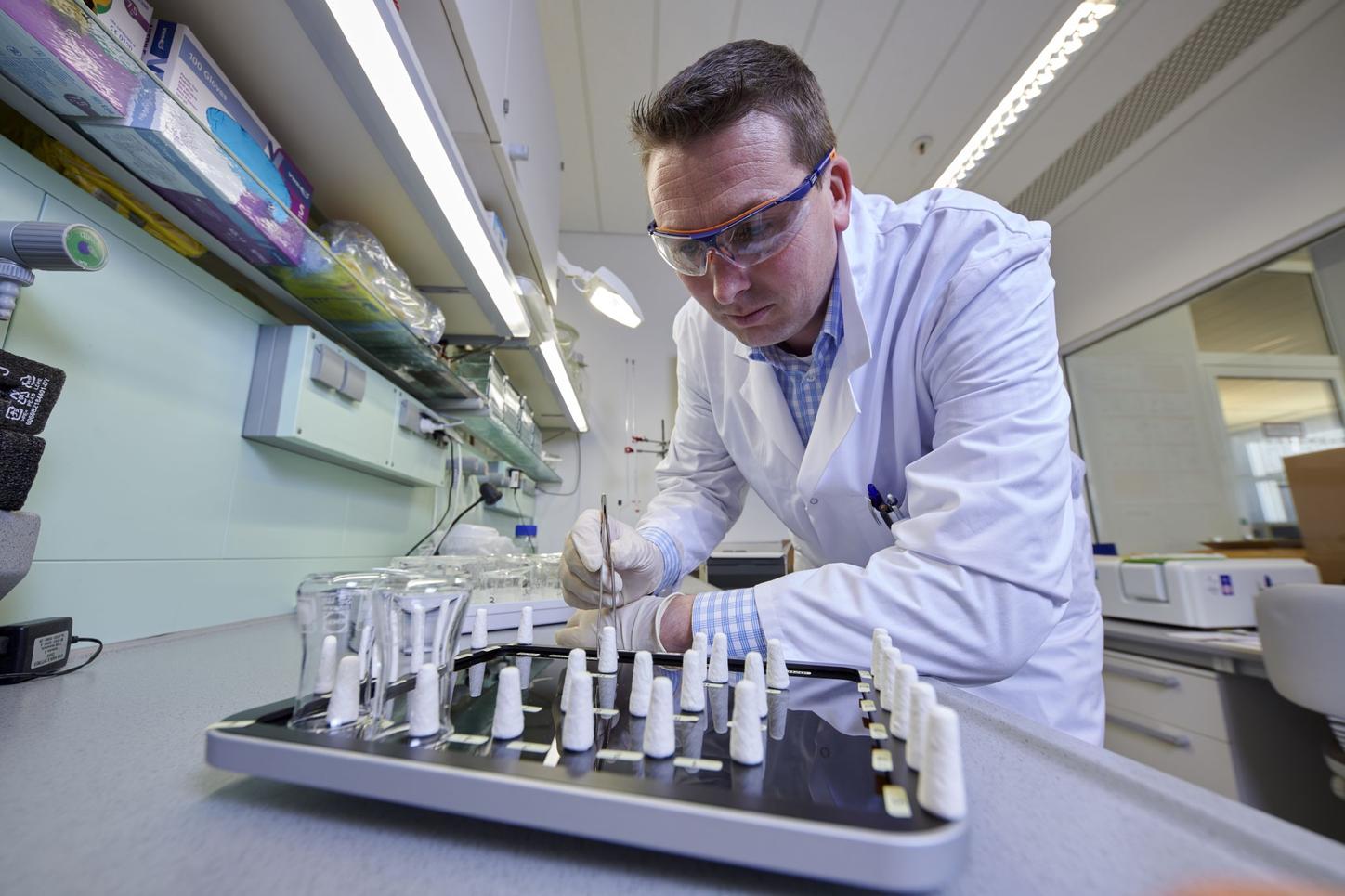
Sebastian Köppl testing a display for its resistance to cleaning agents and disinfectants.
Nothing happens without plastic
<p><a href="Plastic">Plastic</a> is also needed in one other critical area. But it is a completely different type that is put to use here. Andreas Fischer tests the best possible way to use plastics directly within the gradient coils of the MRI scanner. These huge tubes partially turn the magnetic field on and off in a process that facilitates the spatial encoding of the measurement signal.</p>
How do plastics and sustainability go together?
Plastics can undergo mechanical, feedstock or thermal recycling. These processes convert them into new products or break them down into low-molecular substances that then undergo additional processing.
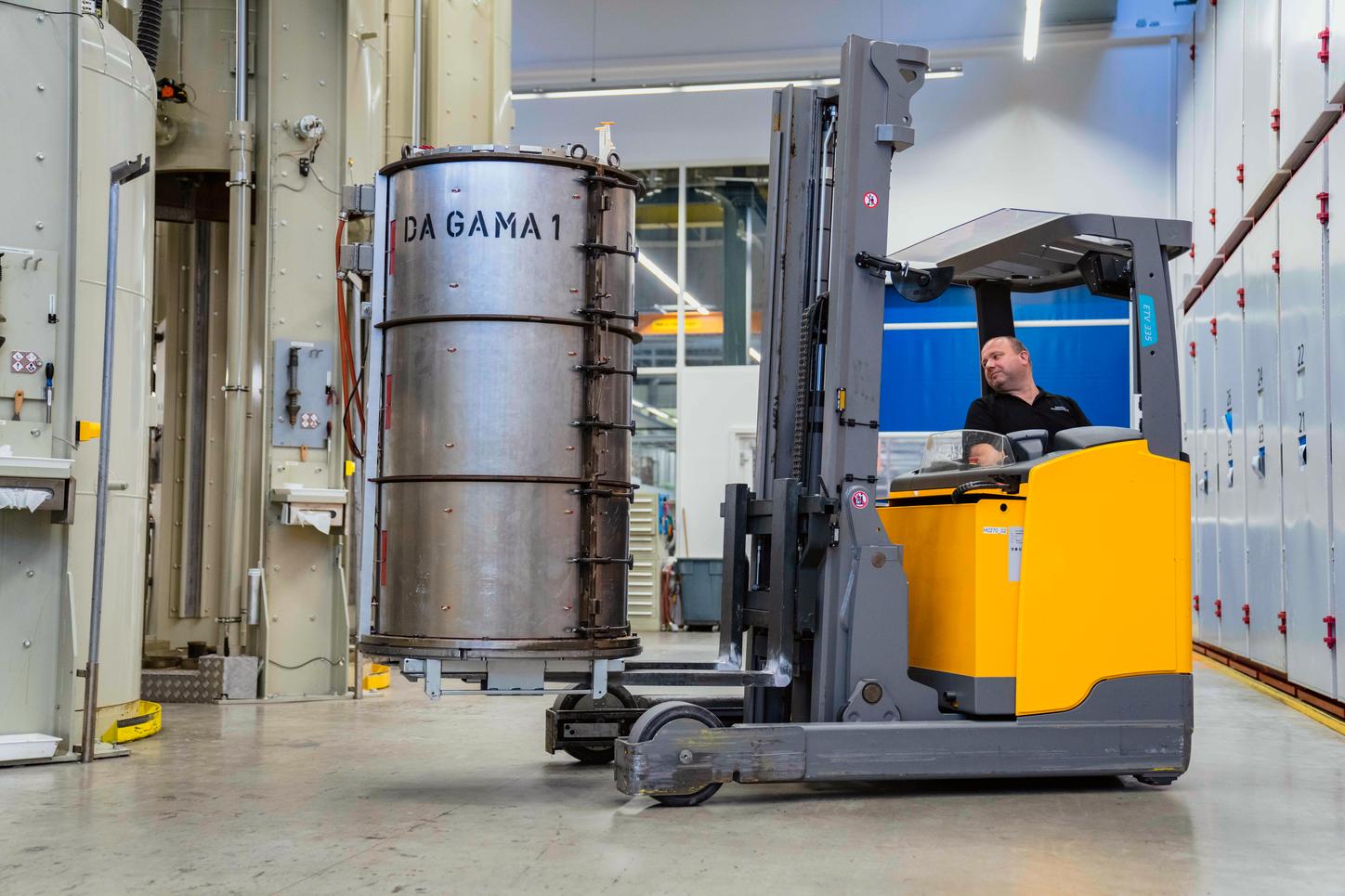
A just-cast gradient coil is driven into a tempering furnace for hardening.
<p>The primary components used in these tubes are copper wires, a cooling system, sensors and the plastic that is used as a casing. They produce the distinctive hammering sound generated by MRI scanners. The coils are impregnated with a resin mixture in vast casting chambers. It is a solution that was developed specifically for this job with the help of resin producers.</p><p>“Plastic is the only material that enables us to keep the coils stable and to safely encase all of the conductors,” Andreas Fischer says. “Our mixture of plastic also dissipates the tremendous heat generated by the coil exceptionally well.”</p>
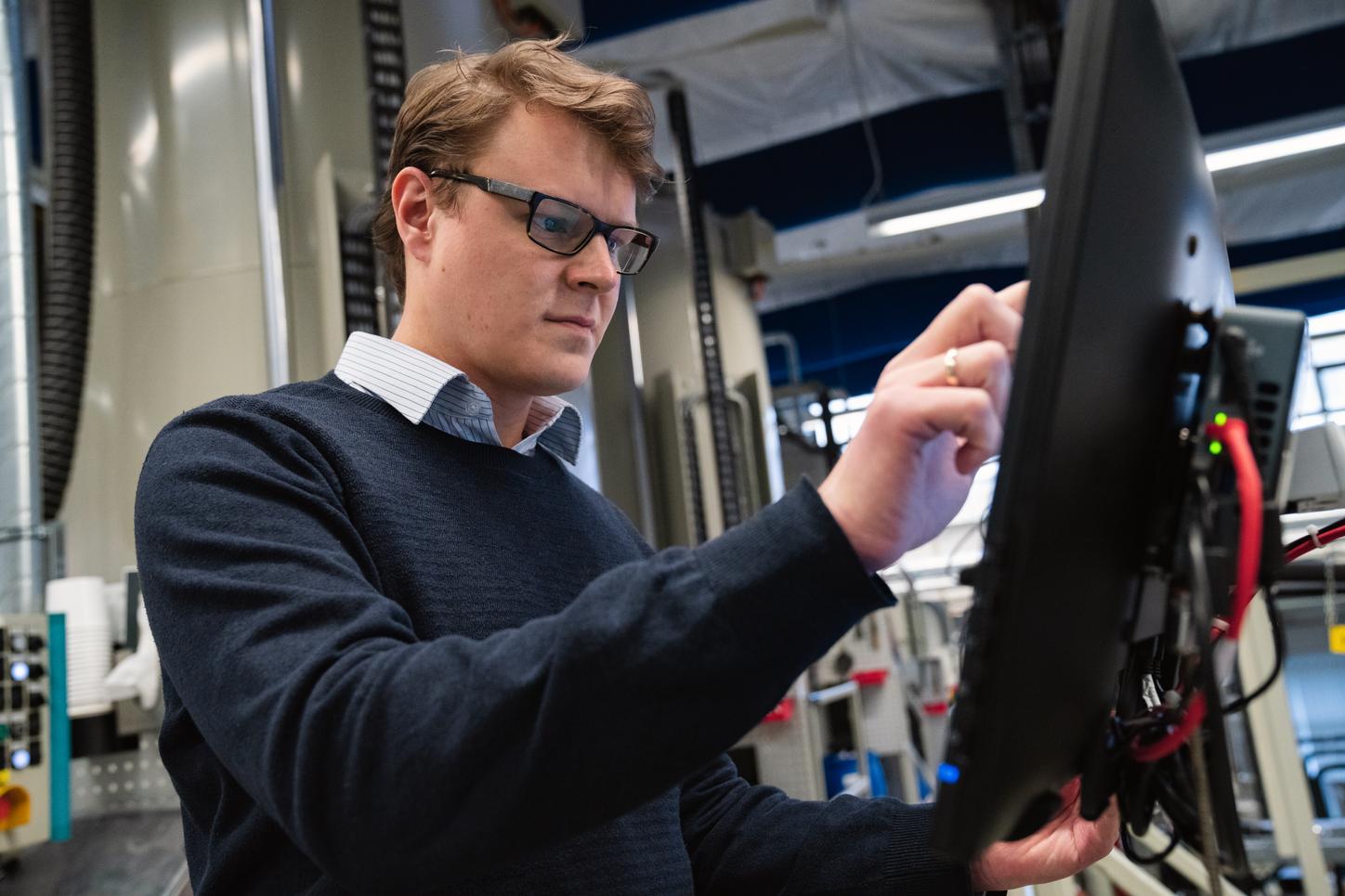
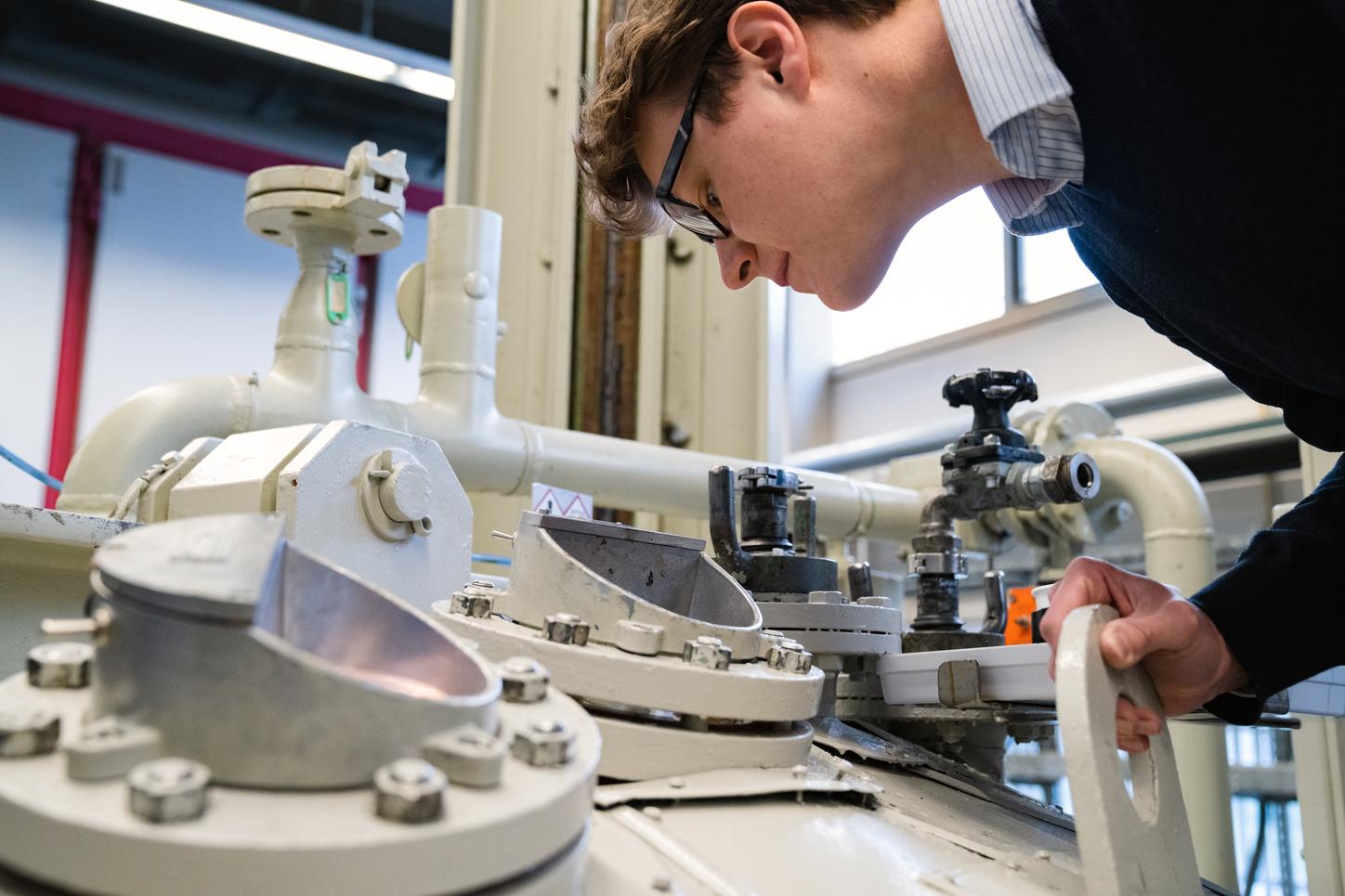
...and makes sure everything is alright in the casting kettle.
<p>After the casting process is completed, the coils are hardened in ovens and then cool down. While Yvonne Candidus does much work by hand – from drawings to prototypes – the processing of the plastics here is fully automated, an advance that put an end to the manual lamination of former times. But the engineer still feels closely bonded with the product: “We conduct all sorts of analysis of plastic and the product itself to produce consistent quality. We do testing to determine the compatibility of our plastic mixture with the other materials used in the coil and optimize the processing parameters.”</p><p>What do Yvonne Candidus, Sebastian Köppl and Andreas Fischer have in common? It is the desire to produce something with their own hands – and to see the result. Sebastian Köppl describes the job this way: “When I see a Siemens Healthineers product at the doctor’s office or on television and I know that I inspected a particular component and checked its safety, then I know exactly why I head off to the lab every day.”</p>
Share this page
By Elena Kleffel
Elena Kleffel is an editor at Siemens Healthineers.
© Photography: Markus Ulbrich
Flexible local coil is currently under development; it is not for sale in all countries including the U.S.A. Its future availability cannot be guaranteed.