- Home
- About Siemens Healthineers
- About Our Manufacturing Sites
- Siemens Healthineers - Sudbury
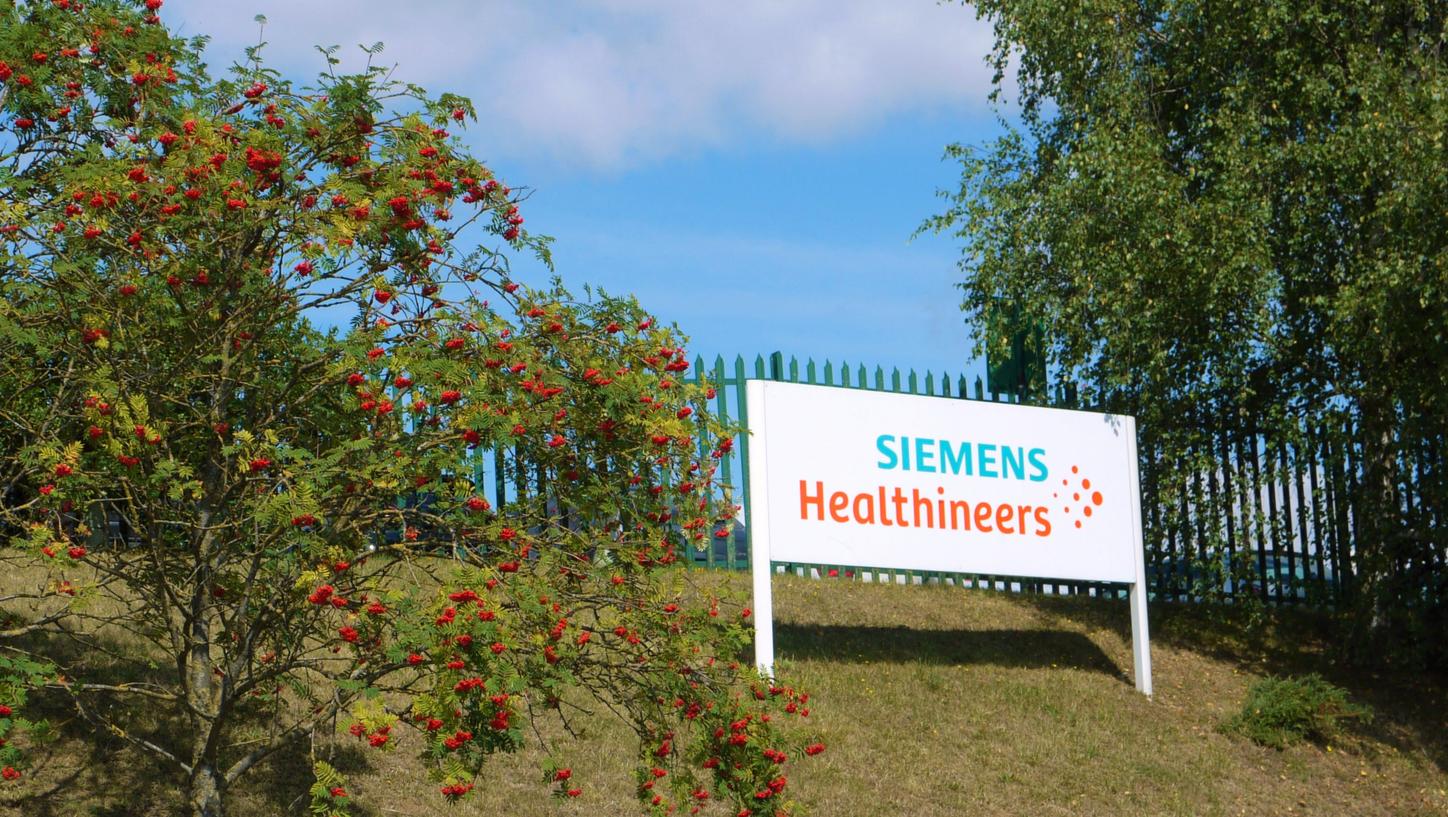
Siemens Healthineers - SudburySudbury is a cutting edge facility which builds instruments and consumables for Urinalysis, Diabetes and Blood Gas analytics.
Sudbury is a diverse site not only in the products we make, but how we run our day to day business with an unwavering focus on Safety First Quality Always at our core. Being one of the only facilities in the Siemens Healthineers network to manufacture and ship instruments and consumables globally, we offer a unique opportunity to everyone in our team to develop and grow.
What We Do
At Sudbury, we are honoured to be a global leading manufacturer in the assembly of specialist instrumentation for laboratories and hospitals across the world for Urinalysis, Diabetes, and Blood Gas analytics. Being the only facility in the network to make and ship these products globally.
This flexible approach and our 85 years history give us the ability to adapt to any opportunity which comes our way, like our response to the 170% surge in demand for our products due to COVID-19, which the team had to respond to whilst adapting to the national lockdown and additional safety measures.
Our site’s achievements stem from our diverse and highly skilled set of employees who are responsible for the production, manufacturing, quality release and shipping of our key technologies including instrumentation, tonometering, pouch filling, blood gas consumable cartridges, reagents, and sensors, along with all support services.
Sudbury is helping lead the way in the adoption of the Healthineers Performance System which develops and implements improvement tools across Siemens Healthineers to become more efficient in our daily processes via running frequent Kaizen events and the onsite promotion of 3i. Facilitating us to create a profound innovative culture where our employees feel empowered to actively challenge the status quo via submitting new improvement productivity ideas using the 3i tool.
We place our employee’s safety and the quality of our products and services at the forefront of our business by championing our own unique motto ‘Safety First Quality Always’, which has seen us gain various accreditations and awards including the British Safety Council Sword of Honour - Health & Safety Award 2012 and Globe of Honour - Environmental Award 2013.
Our time in diagnostics...
Our journey began in 1939 as Evans Electroselenium and evolved into the acquisition by Siemens in 2007, further leading to becoming a part of Siemens Healthineers in 2019.
Since becoming Siemens Healthineers, we have achieved:
2019
- Celebrated 80 years of Medical Device Production
- 5 millionth Wash Waste Cart
- RP500E Launch
- 19 Years of RP400/500
2020
- 16 Years of 1200 Reagent
- 1.5 million AQC Carts
- 2 millionth M-Carts
- COVID- 19 Ventilator challenge
- Head of Point-of-Care facility named as top 100 UK manufacturing professional
2021
- RateMyApprenticeship Award - Top 100 employees and ranked 67th
- Certified as a Great Place to Work™
Careers
'Siemens Healthineers fosters an environment where people can develop personally and professionally...'
A career at Siemens Healthineers in Sudbury means you will be helping to develop truly innovative technology to produce high quality specialised instrumentation for laboratories and hospitals across the world. Individually and as a team, we recognise the vital contribution we make in creating medical equipment that transforms health care and the lives of people across the globe.
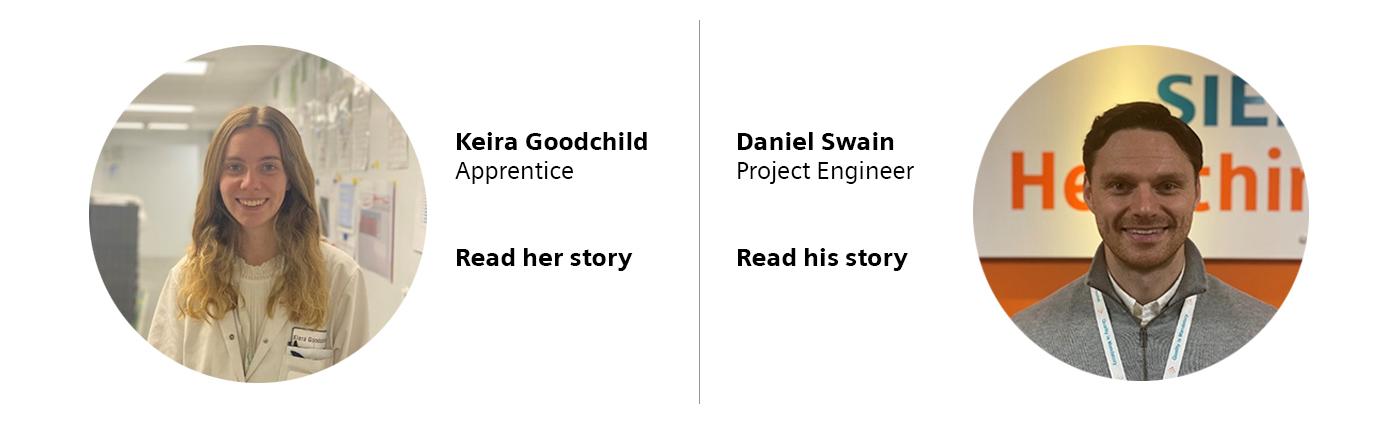
Daniel Swain
Having been with my previous employer since leaving school it was always going to be a bit daunting entering a new place of work for the first time. Add to this the fact that we were in the middle of a global pandemic, it certainly didn’t help any nerves that were there!
Walking through the doors for the first time those nerves were very quickly gone. EVERYONE at Sudbury was welcoming, friendly, helpful; whilst also clearly being focused on their mission to provide quality products to the healthcare industry that were so clearly needed at the time.
To begin with I found the level of the systems and procedures quite overwhelming, but it was something that I braced myself for coming into the medical industry for the first time.
Being a Project Engineer, you are very reliant on the team you have around you to deliver what is required; and the skill level, experience and approachability of my colleagues helps ensure I have the support and knowledge to deliver on what we say we will do.
From a personal standpoint it was refreshing to come into an organisation that clearly supported opportunities for professional development, and in the first year alone I have been on Structured Problem Solving Training and Agile Scrum Master Training.
Another aspect of a job that is important to me is the social and wellbeing side, and before starting I already knew that Siemens Healthineers took this seriously. It’s great to have that time outside of work with colleagues and have some shared downtime from what a fast-paced environment is, especially when it involves winning the yearly Sudbury Site Rounders Competition!
I find that my passion and understanding of our products, processes and industry continue to grow each day. I know there is still so much to learn, and I look forward to what the years ahead will bring as an employee for Siemens Healthineers.
Corporate Social Responsibility
First Responders - working with the local community
We are a local organisation who are prepared to support the local community with retainer staff for all emergency services. We allow permanent employees to be called and to respond to emergencies or disasters with the expectation that all lost time would be expensed by the company. At Sudbury, we have employees that are part of local fire teams, first aid responders and the Military.
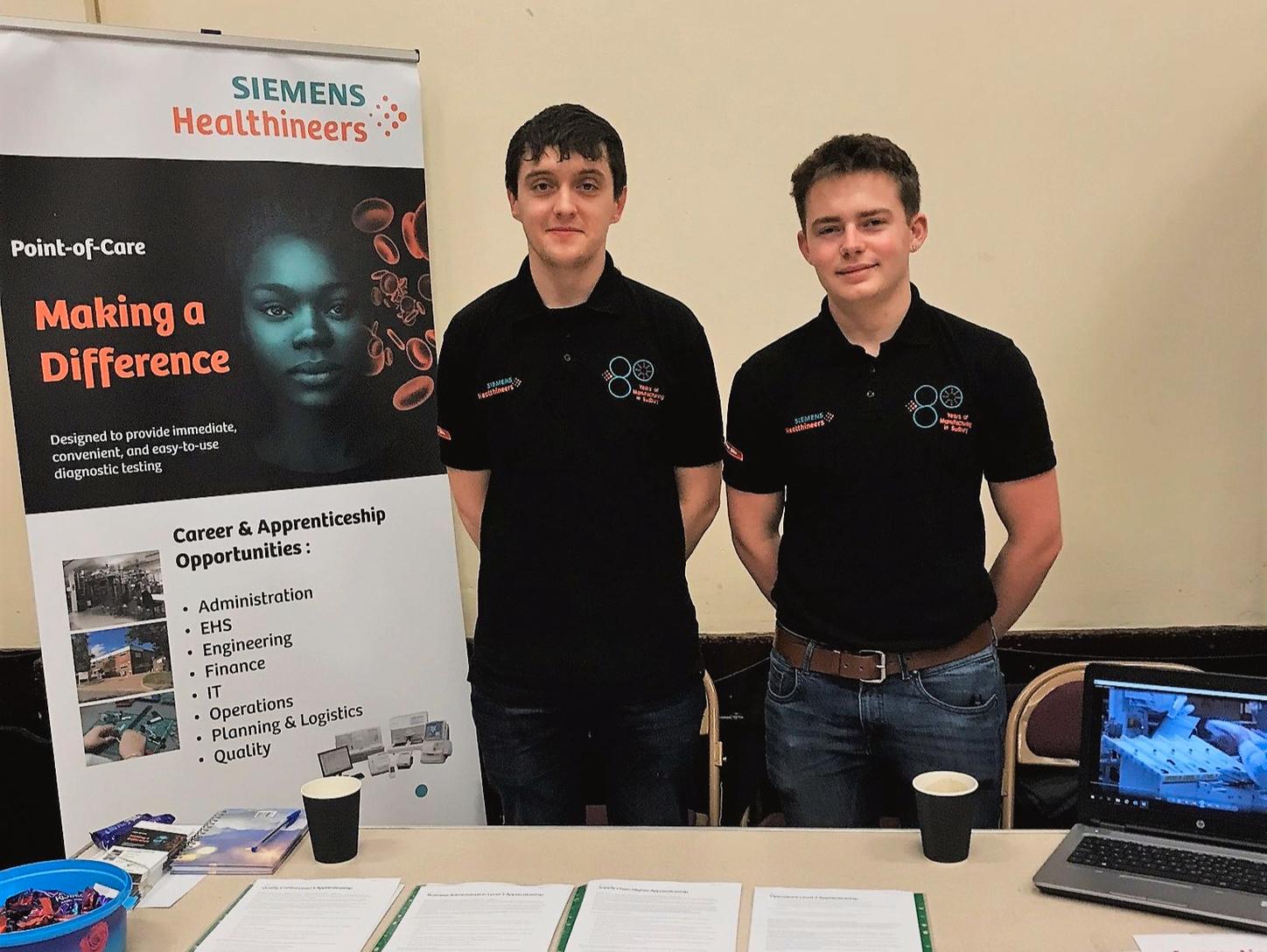
STEM events
As ‘Science, Technology, Engineering and Maths’ are important subjects within the school curriculum, we have supported Science Fairs both in Primary and Secondary Schools. Events have included demonstrations by our Apprentices on the mechanics of our products that we manufacture at the Sudbury site, as well as creating experiments that the children get involved with.
The children all have fun during the events whilst Siemens Healthineers continues to promote its status in the local community. We are keen to encourage employees to become STEM Ambassadors and support CSR events.
Rebuilding local school garden
Siemens Healthineers in Sudbury are keen to volunteer for projects and events within the local area as part of the CSR programme. One Primary School gave us a challenge to ‘tidy’ a garden area.
A team of volunteers from our Leadership Team dug over old flower beds removing weeds and overgrown bushes, before repositioning and ‘fixing’ some existing sleepers to provide a raised area. A local garden centre donated some flowers, so we were able to plant them and provide a peaceful area for the pupils to sit at breaktimes.
First Responders - working with the local community
We are a local organisation who are prepared to support the local community with retainer staff for all emergency services. We allow permanent employees to be called and to respond to emergencies or disasters with the expectation that all lost time would be expensed by the company. At Sudbury, we have employees that are part of local fire teams, first aid responders and the Military.
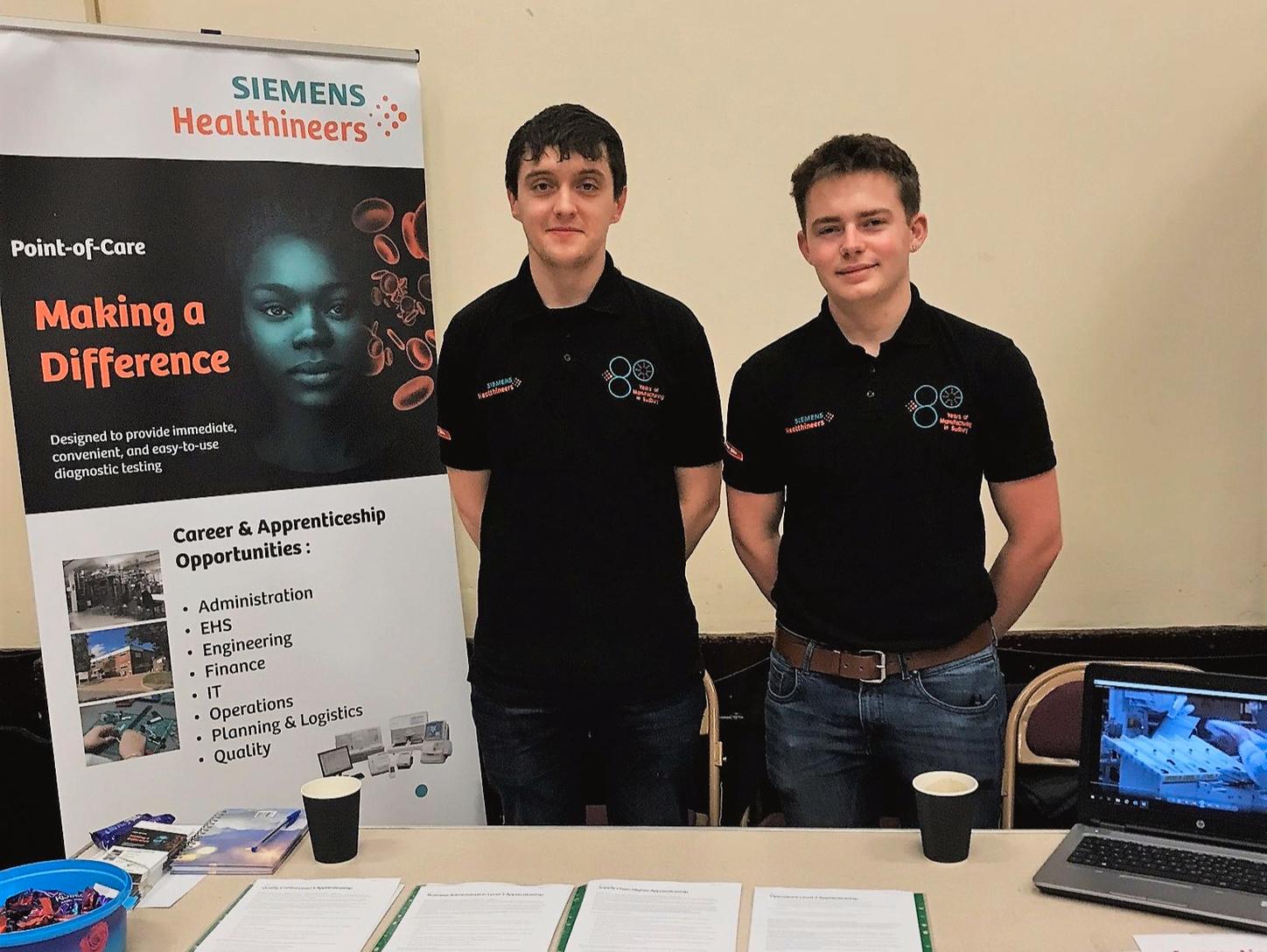
STEM events
As ‘Science, Technology, Engineering and Maths’ are important subjects within the school curriculum, we have supported Science Fairs both in Primary and Secondary Schools. Events have included demonstrations by our Apprentices on the mechanics of our products that we manufacture at the Sudbury site, as well as creating experiments that the children get involved with.
The children all have fun during the events whilst Siemens Healthineers continues to promote its status in the local community. We are keen to encourage employees to become STEM Ambassadors and support CSR events.
Rebuilding local school garden
Siemens Healthineers in Sudbury are keen to volunteer for projects and events within the local area as part of the CSR programme. One Primary School gave us a challenge to ‘tidy’ a garden area.
A team of volunteers from our Leadership Team dug over old flower beds removing weeds and overgrown bushes, before repositioning and ‘fixing’ some existing sleepers to provide a raised area. A local garden centre donated some flowers, so we were able to plant them and provide a peaceful area for the pupils to sit at breaktimes.
First Responders - working with the local community
We are a local organisation who are prepared to support the local community with retainer staff for all emergency services. We allow permanent employees to be called and to respond to emergencies or disasters with the expectation that all lost time would be expensed by the company. At Sudbury, we have employees that are part of local fire teams, first aid responders and the Military.
Snowdon Summit
The Sudbury team took on the challenge to climb Snowdon, the highest mountain in Wales. The Snowdon summit is 1,085 metres above sea level, and there were 13 climbers who in total travelled 537 miles. The team walked more than 24,785 ascending steps each, got lost, but eventually found the summit having completed the climb in 7 hours and 40 mins.
Three Peaks Challenge
The Sudbury team took on the task to complete the Three Peaks Challenge, which involved climbing the highest mountains in Scotland, England, and Wales (Ben Nevis, Scafell Pike, and Snowdon) in one weekend. There was a team of 21 climbers plus a RP 500 instrument. The team travelled 1,247 miles in total and climbed 31 miles of the mountain. They also walked over 80,000 ascending steps each and completed the whole challenge in 36 hours. They broke down once... but still managed to get home!
Peak District Ultra Challenge
The Sudbury team set out to complete the Peak District Ultra Challenge. We had a team of 32 walkers in which; 15 people walked 25km each which totalled to 15.5 miles, 3 people walked 37.5km which totalled to 23.3 miles, 11 people walked 50km which totalled to 31 miles and 3 people walked 100km which totalled to 62 miles. The team walked a total of 831 miles and again broke down... but still got home!
Sudbury to Boston, USA
During the pandemic one employee at Sudbury created a team challenge of trekking the equivalent distance from Sudbury to Boston USA, locally here in the UK. This involved the team peddling, walking, running, and swimming across the UK to achieve the same comparable distance all the way to Boston USA and back to Sudbury totalling 6,586 miles all together.
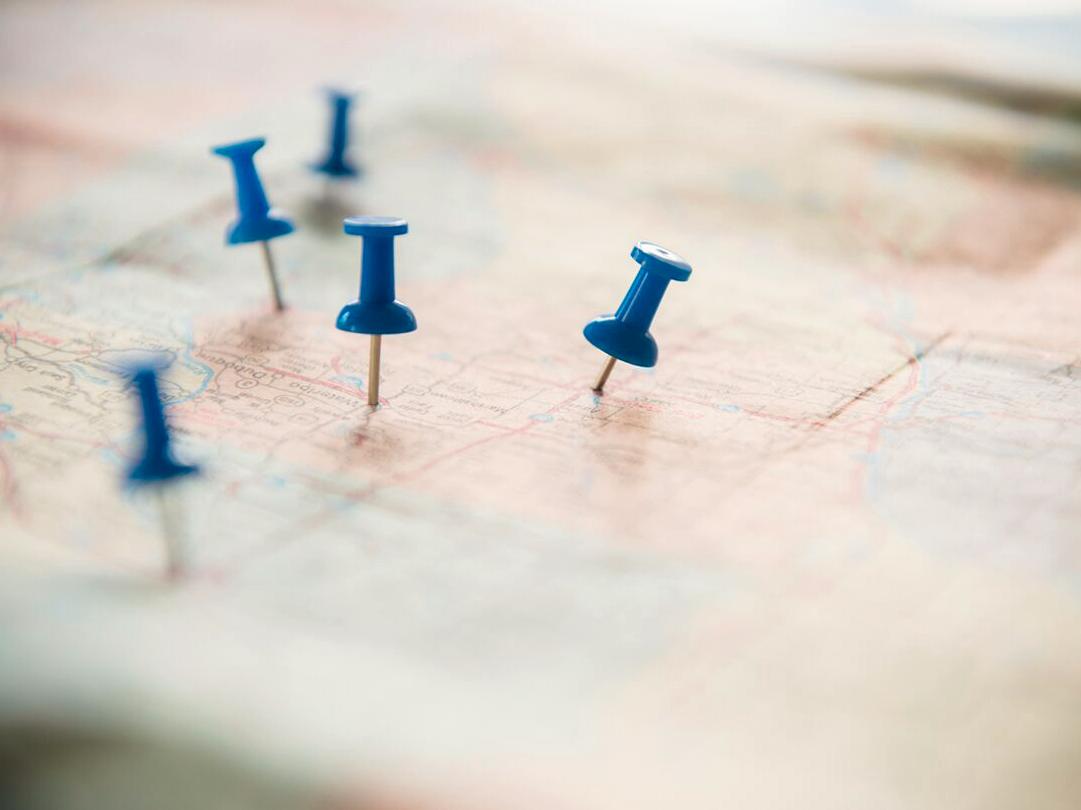