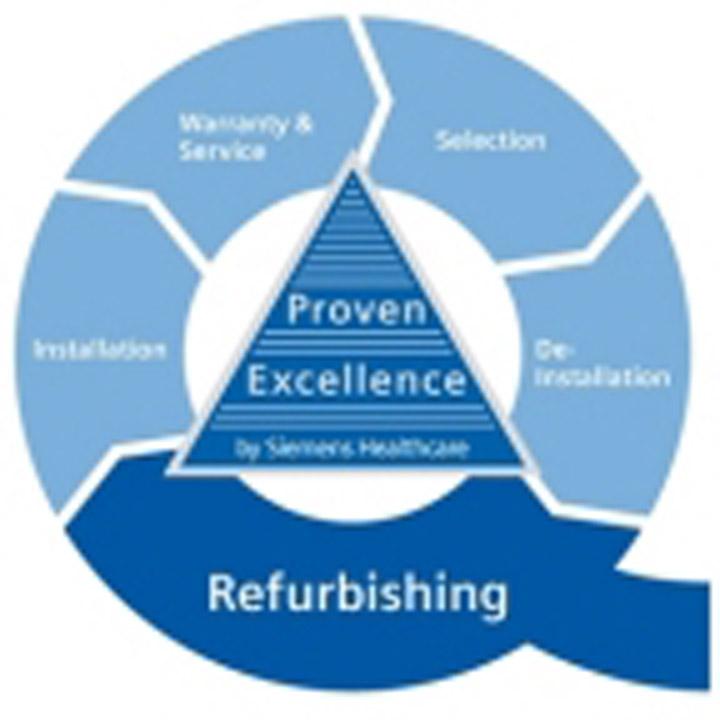
Our process from used medical equipment to high-quality refurbished medical equipment: The Siemens Proven Excellence Program
The Siemens Proven Excellence program with environment-friendly procedures is much more than getting used medical equipment into working condition. It goes well beyond simple quality control to provide performance and new life expectancy to systems refurbished by the original manufacturer with today‘s most-up-to-date original equipment manufacturer spare parts and software.
Learn more about our refurbishing process:
In 5 steps from used medical equipment to Proven Excellence Quality
The excellent quality of our systems is based on an in-depth refurbishing process that all used medical equipment undergo as part of our Proven Excellence program.
This process ensures compliance with Siemens’ high quality standards and also allows us to incorporate innovative Siemens technology.
After completion of the refurbishing process the systems are given our Proven Excellence quality seal. This seal represents the fulfillment of the strict specifications of relevant international norms and standards as well as security regulations.
Step 1 - Selection
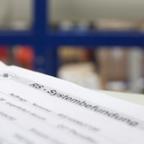
Only the best used medical equipment qualifies! No compromise is allowed when it comes to selection criteria.
- Age and technology level of the system
- Condition, service history and past performance
- Upgradeability of software and hardware status
- Spare parts availability of minimum 5 years
Step 2 - De-Installation
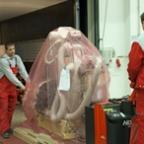
From de-installation to destination, first class all the way!
- Thorough inspection at the customer's site
- Professional de-installation by trained personnel
- Shipping in original packing material
- Transportation to one of the Siemens factories
Step 3 - Refurbishment
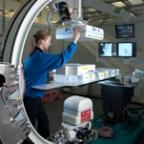
The refurbishment of the used medical equipment begins.
- Cleaning, disinfection and painting
- Replacement of worn out parts with original spare parts
- Thorough checking of components and subsystems
- Software updates to the latest status possible
- Customizing of the systems to the customer's requirements
- Complete system check with original test equipment and procedures
- Application of our Proven Excellence quality certificate
Step 4 - Professional Installation
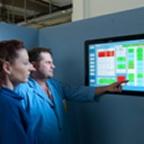
A new life-cycle begins under expert supervision.
- Transportation to the customer's site
- Professional installation by qualified service providers
- Start-up and repeated check-up of the system's performance
- Optional application training
- Handover of original user documents and our Proven Excellence quality certificate
Step 5 - Warranty & Services
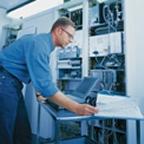
A lasting and successful partnership.
- Warranty typically equivalent to a new system
- Spare parts available for minimum 5 years
- Flexible financing solutions and service contracts
- Worldwide qualified contact partners
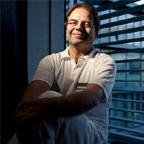
An ecoline success story
Learn about the benefits of used medical equipment
"Used instead of new equipment saves us costs of almost 30 percent. This enables us to offer our patients a comprehensive range of high technical performance and diagnostic capabilities."
Steffen Klengel, MD,
Director, Medical Care Center (MCC)
RadCom GmbH, Riesa, Germany
Steffen Klengel, MD, head of the Medical Care Center RadCom GmbH, in Riesa, Germany, is the first Siemens customer worldwide to have ordered a magnetic resonance system (MRI), a MAGNETOM® Symphony, that has been refurbished through a new scalable refurbishment offering. Using this process, he was able to choose specifically which refurbishment options he wanted, and which he did not, for his new purchase.
Read more