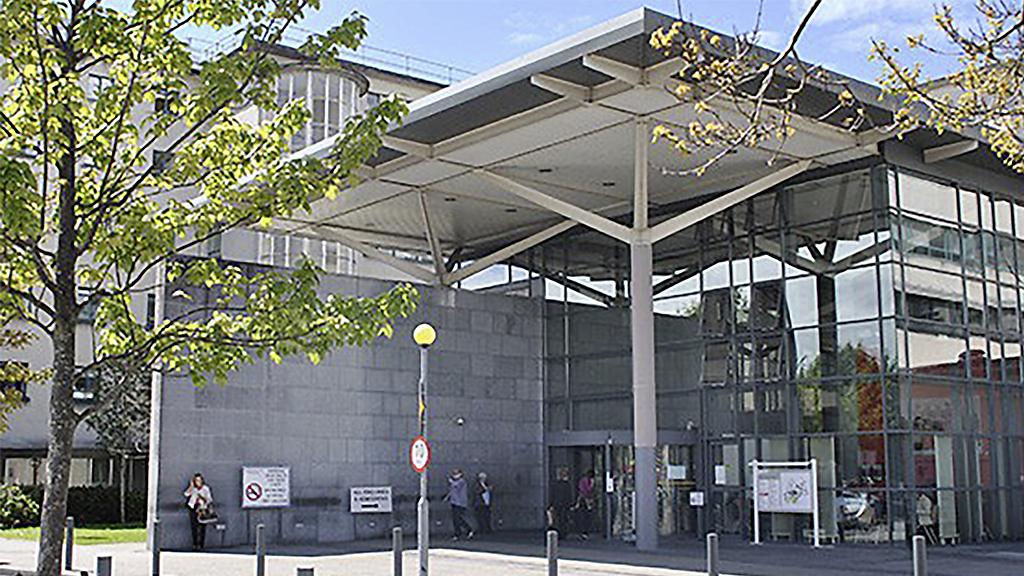
Not years. Not months. Just days to achieve a better working environment and an improved patient experience. In less than 30 days, the staff at University Hospital Galway in Ireland implemented changes that led to sustainable clinical and operational improvements in their radiology workflow. Today, the results are tangible and frequently perceived by their patients and personnel onsite.
Download case study here.
The staff at University Hospital Galway (UHG) in Ireland, part of the Saolta University Health Care Group, wanted to increase the efficiency of their radiology workflow. Constraints in Ireland’s hospital system, along with high management turnover and the involvement of multiple stakeholders for each patient examination were leading to cancellations, unprepared patients, additional delays, and a growing waiting list. The hospital management recognized the need for external professional expertise and services to positively impact the working environment and better support the staff to provide timely diagnosis and treatment. They realized this would ultimately benefit their most important stakeholder - their patients.
Addressing existing opportunities through Rapid Improvement Events
To remain competitive, provide high quality care, and ensure an improved and positive patient experience, UHG wanted to hire external professionals to make additional changes to their existing processes. However, in order to achieve lasting improvements, they first needed to improve communication and collaboration between stakeholders while motivating the staff to embrace a culture of change and continuous improvement. In an over-600-bed hospital and complex organization such as this one, generating permanent changes with long-lasting positive impact can take months, and in occasions, even years. To drive fast and sustainable change, UHG decided to call upon the expertise of the Siemens Healthineers Enterprise Services consulting team.
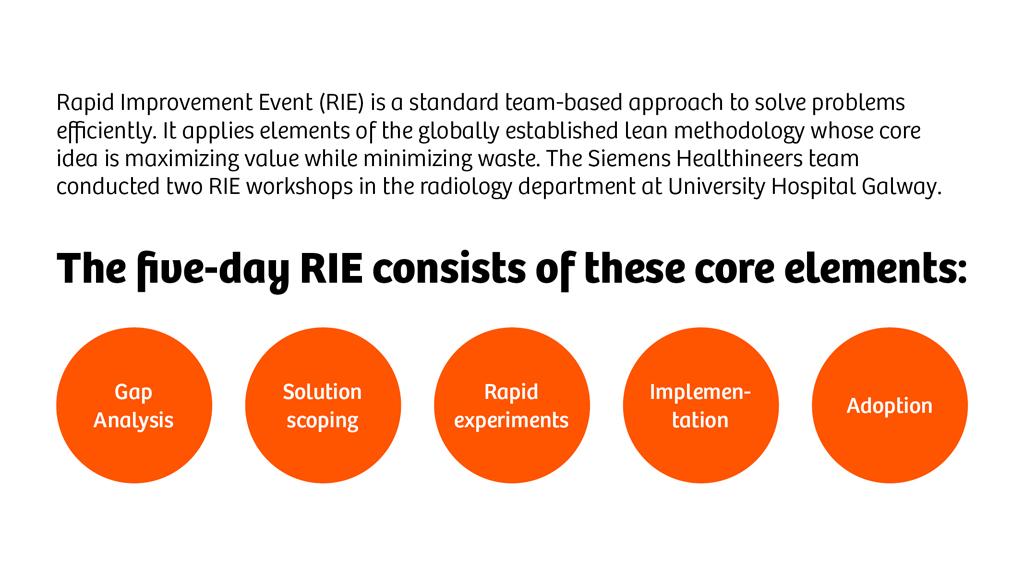
Based on the principles of lean and a detailed transformation plan, the consulting team, together with the hospital staff, applied a methodology named Rapid Improvement Event (RIE). They conducted two five-day RIE workshops to identify superfluous activities and define desired improvements and results in the areas of computed tomography (CT) and interventional radiology (IR). Their goal was to quickly streamline scheduling and patient preparation processes in order to eliminate resource waste, improve the working environment, and deliver increased value to the patient.
Fast results that make a real difference – to the patient and staff
Siemens Healthineers Enterprise Services consulting team defined and adopted a set of solutions and standard procedures to improve communication and collaboration. For example, “CT hubs” were implemented in standardized locations on dedicated wards. Equipped with a patient-preparation checklist and the necessary contrast agent, the hubs made it easier for the ward staff to prepare their patients. This helped provide a smoother process for both patients and staff, and it reduced delays. The team also restructured CT scheduling to accommodate staff availability and reduce waiting times. In IR, the team implemented new processes and policies for transparent scheduling, and a concept for proactive patient handover.
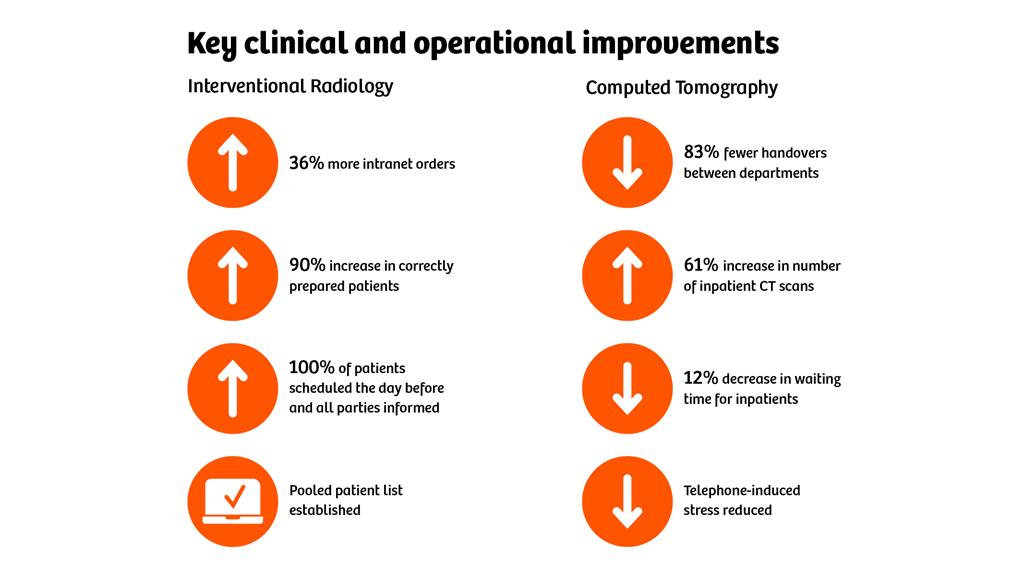
In only a few days, the hospital noticed positive operational and clinical results that are fostering an improved working environment for the staff, leading to lasting improvements in patient experience. For instance, the average number of interactions per patient between radiology and ward staff decreased from 41 to 7. This has helped improve working relationships and freed up time for staff to focus on other topics. Further, the average number of inpatient CT scans increased from 33 to around 53 per day, and the waiting time from request to scan for priority two and three inpatients dropped from an average of 52 hours to around 46 hours. These improvements mean reduced waiting time, translating to earlier diagnosis and greater peace of mind for patients.
New streamlined processes in IR enable a more proactive approach to patient preparation: In the past, only 50% of patients were correctly prepared. Today, this figure is 95%. This facilitates a smooth and timely start in the morning with fewer delays during the day. Combined with the new scheduling process, which is more flexible and transparent than the previous process, the waiting list has been reduced to almost zero. Through the improved preparation process, the hospital is able to reduce errors, which has led to a lighter workload for the staff.
“The Rapid Improvement Event approach of Siemens Healthineers triggered significant change and solved problems I had thought were here to stay.”
UHG staff members are proud of what they have achieved and believe that the Rapid Improvement Events implemented have helped them transform care delivery and improve patient experience. Following a 30-day evaluation, the organization verified that the initial results are sustainable. “The Rapid Improvement Event approach of Siemens Healthineers triggered significant change and solved problems I had thought were here to stay,” concludes Dr. John Bruzzi, Clinical Lead of Radiology at UHG. Underscoring his optimism was the recognition for best clinical audit poster presentation during the Multi-Disciplinary Research, Clinical Audit and Quality Improvement day at Galway University Hospitals. The organization is confident the changes, which led to new standards and procedures, will continue to allow them to provide a positive working environment and patient experience.
About University Hospital Galway
University Hospital Galway was founded in 1924 and is one of the main teaching hospitals for the Medical School of National University of Ireland. The hospital has over 600 beds and treats about 65,000 patients per year. It is based in Galway at the Irish West Coast.