This statement sets out the actions taken by Siemens Healthcare Pty Ltd to address modern slavery risks in our business and supply chain.
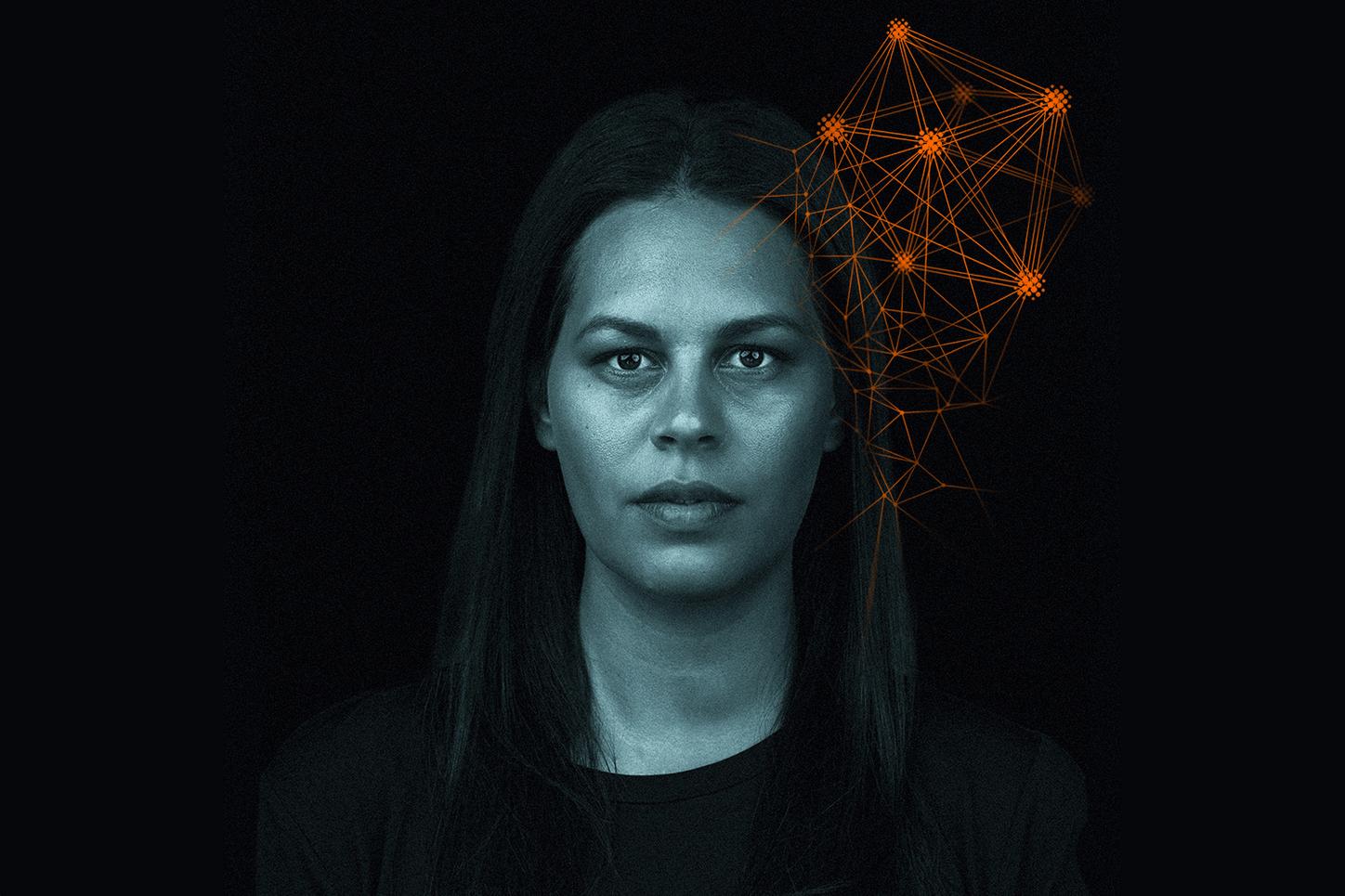
This statement sets out the actions taken by Siemens Healthcare Pty Ltd to address modern slavery risks in our business and supply chain.