Siemens Healthineers has helped diagnostic laboratories leverage the benefits of automation and IT since 1998, making workflow more efficient and flexible while improving turnaround times, reducing errors, and cutting costs. Explore the reasons behind Siemens Healthineers leading role in laboratory automation. We’ll help you transition to improved laboratory management.
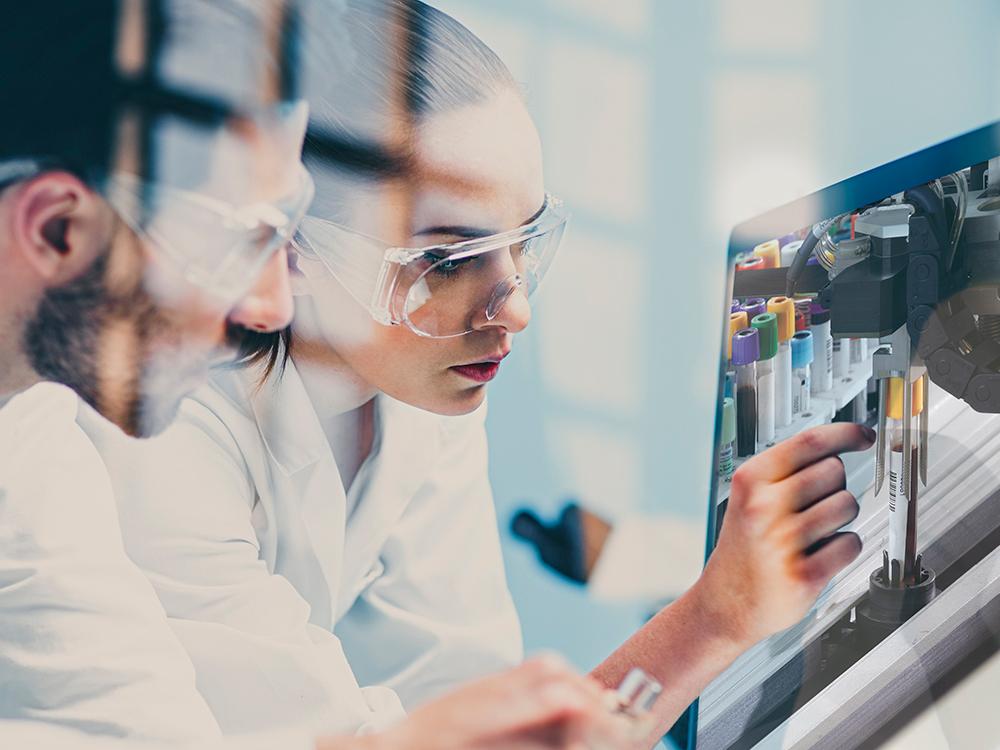
ARUP Laboratories and Inpeco Group discuss emerging technologies to automate disciplines, specialties, and processes both inside and outside the lab. Learn how these innovations can help you improve efficiency, productivity, and accuracy.